ERP Solutions
for the Food & Beverage Industry
Fill out the form to request information
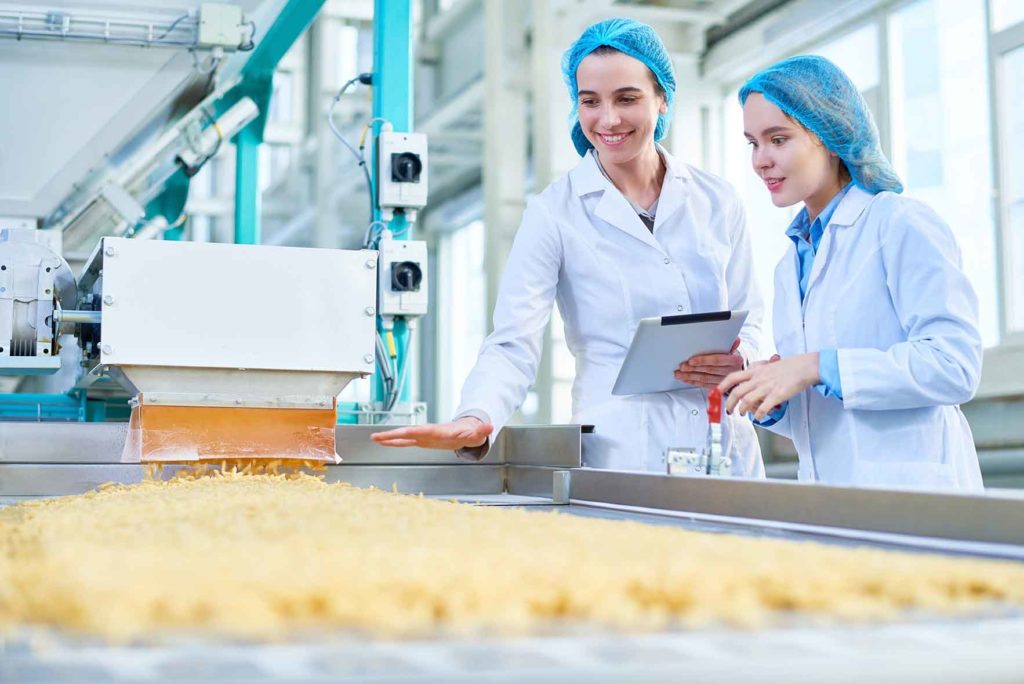
Download the Brochure Food Industry
An ERP Solution to Simplify the Complexity of the Food Industry
Implementing an ERP system that efficiently and securely manages every step of the production cycle while fully complying with the strict regulations of the food industry is essential for businesses in this sector.
The food industry demands full traceability of raw materials, from their arrival at the warehouse to the monitoring of production, transformation processes, and final sales. Additionally, companies must manage production, logistics, sales, quality control, financial operations, and inventory—all through a robust ERP platform.
Managing perishable goods with ERP software is crucial for ensuring operational safety and regulatory compliance in both distribution and production.
ERP systems provide end-to-end support for perishable goods, enabling real-time tracking of expiration dates, inventory levels, and storage conditions. This helps businesses optimize order planning, reduce waste, and ensure products are sold before they expire.
Traceability is a critical requirement, ensuring every perishable product is fully identifiable and trackable, both within the organization and across the entire supply chain. ERP solutions enable precise tracking of production batches and inventory, streamlining data management to uphold food safety and product quality.
For businesses with multiple locations or retail outlets, ERP systems deliver centralized inventory and operations management. This enhances cross-department communication and supports smarter resource planning, driving efficiency and scalability across the organization.
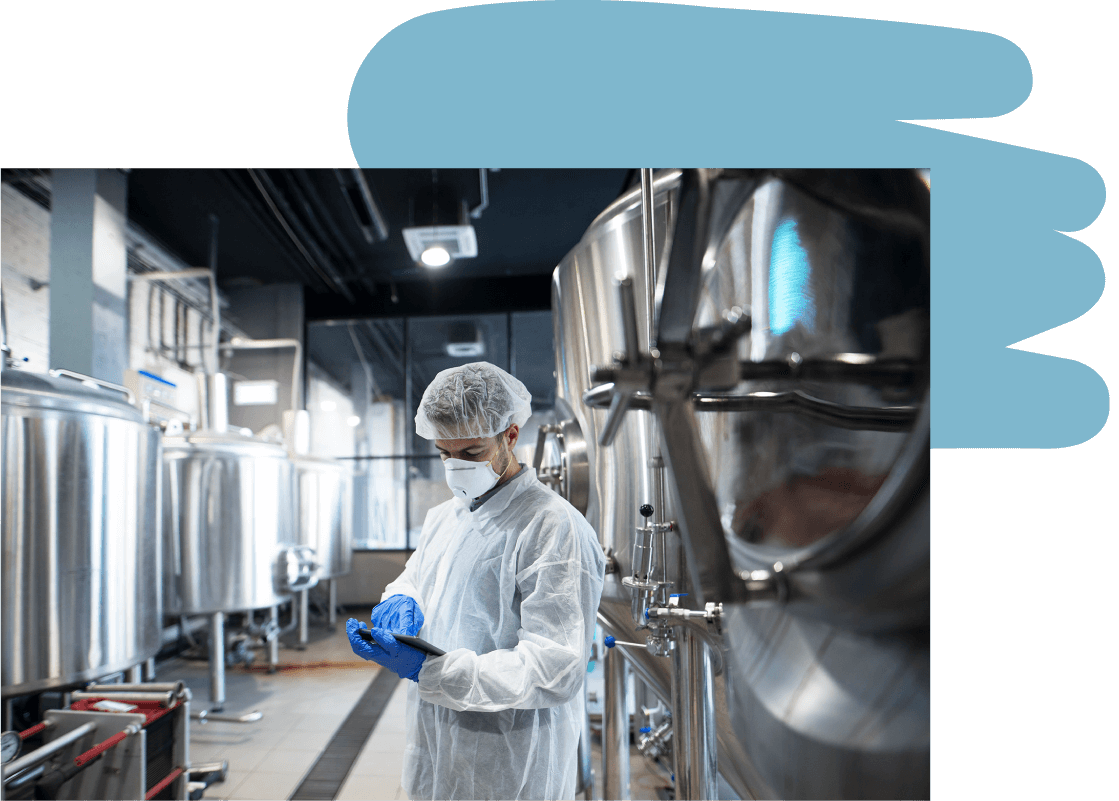
Fluentis ERP Food Industry: Make to stock & Make to Order in Compliance with Food Law
Fluentis ERP Food & Beverage è una soluzione completa ed integrata, studiata per accompagnare le aziende del settore alimentare nel delicato processo di innovazione e miglioramento delle performance.
Fluentis ERP Food & Beverage is a complete and integrated solution designed to support food industry companies in the delicate process of innovation and performance improvement.
An innovative ERP system capable of combining advanced technology with industry-specific expertise, it is highly configurable thanks to the flexibility and efficient parameterization of the software. This makes it adaptable to small, medium, and large companies, with the goal of ensuring high levels of production efficiency while guaranteeing strict product safety standards.
The management of EDI (Electronic Data Interchange) is a crucial aspect for optimizing and automating communication between the stakeholders (customers and suppliers) in the food supply chain.
EDI is a standardized system for electronically exchanging business documents such as orders, sales slips, invoices, and related records. In Fluentis, through the processing of standard XML files, integration is possible with providers responsible for handling EDI-formatted files.
The integration between ERP and EDI management provides the following advantages:
Process automation: EDI integration automates the transmission and processing of business documents among the various companies in the supply chain, reducing manual intervention, minimizing data entry errors, and improving overall efficiency.
Speed and timeliness: EDI allows for the instant transmission and receipt of documents, speeding up order processing and reducing delivery delays.
Traceability: It is possible to track the status of orders, shipments, and invoices in real time. This visibility helps improve supply chain management and provides customers with more accurate delivery information.
Regulatory compliance: The food industry often faces strict regulatory and safety requirements. Using EDI helps ensure compliance and simplifies the management of the information needed to meet current regulations.
Cost reduction and sustainability: Automating these processes can lower operational costs by reducing the need for printing paper documents, shipping, and manual data handling.
Data security: Through dedicated FTP areas, it is possible to store incoming and outgoing files securely.
Are you in the Food & Beverage industry and facing a specific challenge that's impacting your efficiency?
See what we can do for you
Send us your RequestStrengths of the Fluentis ERP
Food Industry Solution
Production, Planning, and Sales Processes
- Product specification (ingredients)
- Management of weight variants and dual units of measure
- Management of bill of materials, percentage-based recipes
- Management of processing stages and enhanced production planning
- Production scheduling (Make to Stock, Make to Order)
- Management of work cycles by line, work center, or machine
- Management of product seasonality
- Batch-based production management
- MPS and MRP planning (including finite capacity)
- Integration of production devices
- Integration of production and sales processes and demand forecasting
- Monitoring of product perishability
- Immediate reconciliation of weights directly within the system
- Estimated cost calculation for items and actual processing cost tracking
Backflushing
- Accounting system that applies production costs only when the production completion percentage reaches 100%
- Management of both internal food production and outsourced production
- MES (Manufacturing Execution System)
- Availability analysis and automated production order proposals, along with automatic supply management
- Production proposals based on recipes, for primary or alternative production lines
- Production withdrawals via barcode scanning with expiration date analysis and batch management
- Interface with scales and label printers
- Multidimensional statistics for direct and indirect production costs
EAN 128 Barcode Management
- Electronic product identity card
- The barcode contains information about the batch, item, and description to trace the origin and reconstruct the product history
- Security and logging of the product line, from raw materials to market release
- EAN for material batch, product batch, packaging, and pallet
- Secure management of product label printing with corresponding logging
Warehouse and Logistics
- Weighing and labeling
- Monitoring material flow
- Reducing stock and managing empty containers
- Delivery schedule planning and transportation cost optimization
- Pallet and container management
- SSCC label and container management
- Picking and packing lists
- Automatic generation of picking lists through automatic availability and expiration date analysis
- Integrated warehouse management with RFID radio frequency devices
- Inventory management and supply chain tracking
- Dual “real” unit of measure
- Automated warehouses
- Batch management and expiration dates, FIFO (First In, First Out) and FEFO (First Expire, First Out)
- Monitoring product delivery and production orders that pull raw materials from the warehouse
- Product expiration calculation and expiration-based product analysis
- Yield control
- Specific functions for warehouse management of products requiring portioning (e.g., meats), packaging (e.g., fish), legal labeling, and products requiring dual unit of measure management or time-based pricing.
Sales and Agent Support Area
- Synchronized management of commercial processes and the GDO (Large-Scale Distribution) channel
- Management of retail points of sale, both directly and via FTP import/export of relevant information
- Management of rewards, incentives, and gifts
- Agent commission management
- Cascading discounts, campaign and promotion management
- Price list management per customer/product
- Workflow, parametric controls on the sales order entry and authorization process
- Assortment management with the option to select only available items from the catalog for the customer
- Integration with major EDI standards
- Integration with SFA (Sales Force Automation) for sales attempt tracking
- Cost and raw material consumption reports
Integrated CRM for Order Collection
- Order acquisition via the web
- Order collection via terminal for sales agents
- Integrated cloud-based CRM
- Post-sales support
- Management of agent expense reimbursements
- Electronic invoicing
- Sending communications to customers, suppliers, and prospective companies based on common tracking systems used by Large-Scale Distribution companies (e.g., Indicod, Filconad, Edifact, etc.)
Incoming and Outgoing EDI
- Process automation
- Speed and timeliness
- Traceability
- Regulatory compliance
- Cost reduction and sustainability
- Data security
Management Control and KPI (Key Performance Indicators)
- Reduction of organizational, production, and labor costs
- Cost tracking and inventory management
- Customer and product analysis and statistics
- Margin and profitability analysis
- “What if” scenario simulations
- Improved information sharing among users through access to the contact database
Quality, Food Law CE 178/2002
- Operational workflows are natively integrated with the company’s quality management system
- Compliance with “food law” and food and environmental safety regulations
- Management of security and password protocols within the ERP system
- Quality controls during product acceptance and throughout the production process
- Generation of product Analysis Certificates and Certificates of Conformity
- Management of complaints and non-conformities
- Business Intelligence tools for production and quality control
See What Our Customers Say
No references available
Discover how Fluentis ERP
can transform your business
15-day free trial | No automatic renewal | Instant access
Contact us for more information
Get in touch with us if you:
- Are a SMB in Manufacturing, Distribution, or Services
- Need to streamline and digitalize your business processes
- Want to take advantage of the benefits of a native cloud solution
- Want to replace your non-integrated softwares with a unified ERP platform
+1 281 404 1726
Chat with us