ERP Solutions
for the Electrical and Electronics Industry
Fill out the form to request information
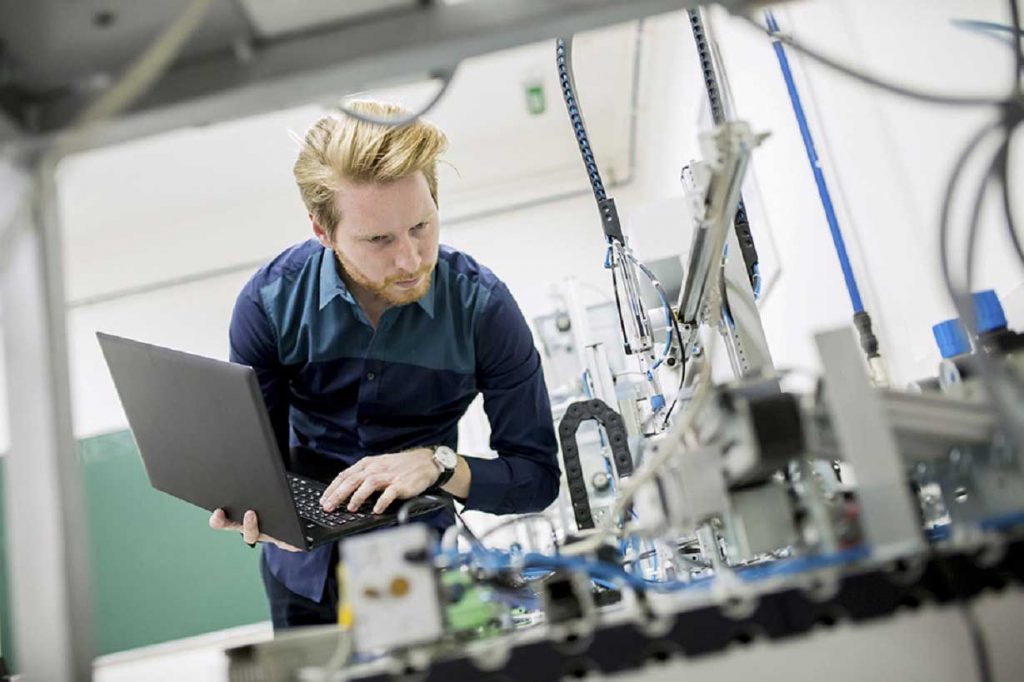
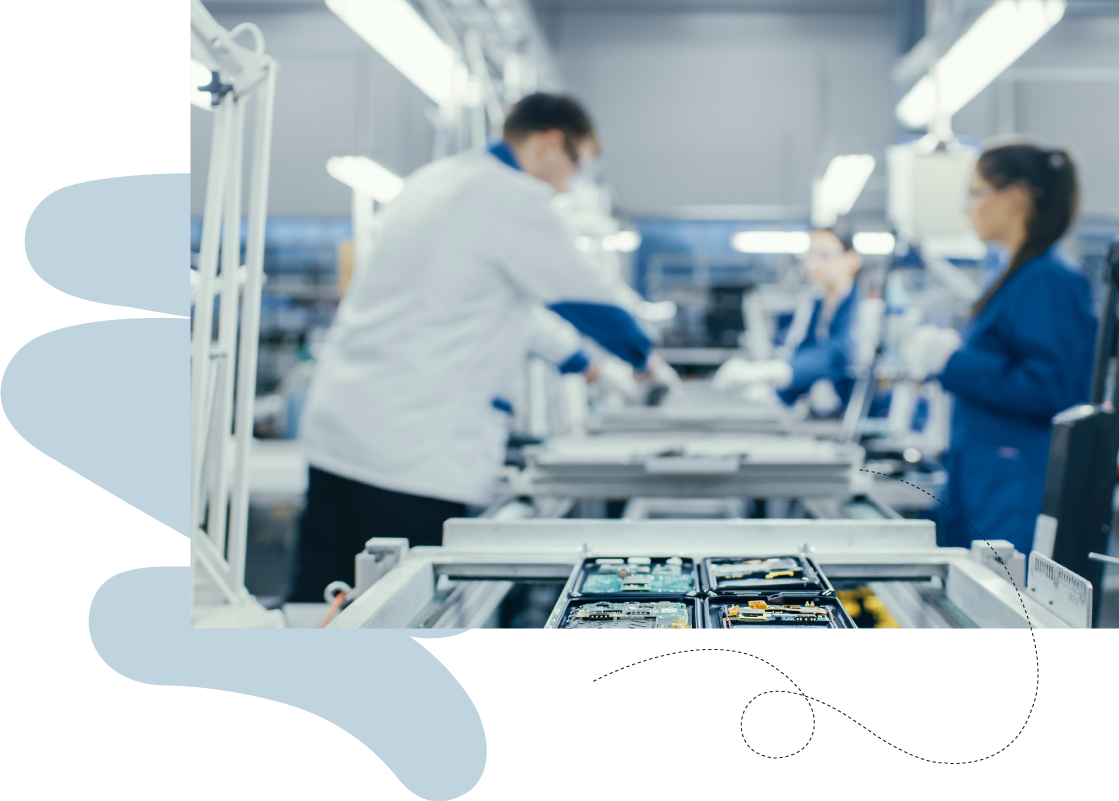
The ERP Solution for the Electrical and Electronics Industry
Fluentis ERP provides a specialized solution tailored to the unique requirements of the Electrical and Electronics sector, developed in collaboration with leading industry partners.
EDI Standards, such as ANSI X12 or GS1, ensure seamless document exchange for order management, invoicing, and shipping. Fluentis ERP supports these standards to automate and standardize processes, streamlining operations for businesses in the industry.
WEEE (Waste Electrical and Electronic Equipment) management capabilities are fully integrated into Fluentis ERP, providing robust tools to ensure regulatory compliance and efficient waste handling.
Strengths of Fluentis ERP for the Electrical and Electronics Industry
Critical Phase Planning
Managing Wait Times in Production Cycles
Grouped Bill of Materials
Outsourcing and Home Workers Management
Batch/Serial Number Management
Actual Product Cost
Delivery Delay Management
Industry 4.0
Customer/Supplier Scoring
EDI
External Assembly/On-Site Assembly
Integration with Automated Warehouses
Prototype Management and Approval Workflows
Critical Phase Planning
In the electrical and electronics industry, production often relies on scheduling based on the availability of critical work centers. Fluentis ERP provides tools to plan around the critical phase, enabling the system’s algorithm to automatically schedule all subsequent phases of the workflow.
This approach ensures that planning for the critical phase triggers a cascading “pull” logic to optimize the scheduling of other tasks. It maximizes the utilization of work centers and labor groups involved, ensuring a streamlined and efficient production process.
Managing Wait Times in Production Cycles
For production workflows that alternate between internal and external phases, accurately tracking wait times is critical. These metrics empower businesses to devise effective cost strategies and enhance overall process efficiency.
Fluentis ERP allows users to assign specific wait or queue times to each phase in the production cycle. These times can later be analyzed through post-process reporting, offering actionable insights to identify bottlenecks and streamline operations.
Grouped Bill of Materials
Managing a multi-level bill of materials (BOM) is essential for effectively handling semi-finished products in inventory. Fluentis ERP enables grouping within the BOM, such as by wire/cable type or color, to streamline specific production phases like cutting operations.
Outsourcing and Home Workers Management
Managing outsourcing and home-based workers is essential in this sector, allowing real-time updates on production progress. Outsourcing partners and home workers are assigned their own production capacity, and with the planning tools in Fluentis ERP, external work phases and the necessary materials can be easily and quickly allocated.
The system allows businesses to track the availability of external resources at any given time. Alerts are triggered when the minimum stock level of components at external warehouses is reached.
This ensures that the management of external resources is always under control. At the end of the month, or according to the billing period, businesses can generate reports to recognize the work completed by home-based workers.
Batch/Serial Number Management
Production in this sector often follows a batch or serial number system. Fluentis ERP ensures complete traceability of production, both forward and backward. It allows users to quickly and easily query the serial number or batch of an item to view its composition, whether by batch or serial number.
Similarly, users can track the serial number or batch of a component to determine where it has been used in the production process.
Actual Product Cost
The management of work cycles and real-time production reports enables the creation of a dashboard that highlights, through a traffic light system, the gain or loss in production. For each production order, it is possible to view the estimated material costs and labor costs, compared with the actual material costs and labor costs, along with the corresponding percentages.
Delivery Delay Management
The production planner, as well as the responsible sales representative, always have access to a tool that highlights any delivery delays in real time, based on production reports. This allows the delay to be confirmed and, through a workflow, an automatic email can be sent to the end customer, indicating the new delivery date.
Industry 4.0
The interconnection between Fluentis and Industry 4.0 machines is a key element for optimizing and driving the digital transformation of industries. Industry 4.0 is defined by the integration of digital technologies into production processes.
With the interconnection between Fluentis and Industry 4.0 machines, companies can achieve greater operational efficiency and a more intelligent management of resources. Fluentis acts as the “core” of the business, managing activities such as resource planning, order management, inventory, accounting, and more.
Learn more
The integration between Fluentis and Industry 4.0 machines is a key factor in optimizing and digitally transforming manufacturing operations. Industry 4.0 is characterized by the incorporation of digital technologies into production processes.
With the connection between Fluentis and Industry 4.0 machines, companies can achieve greater operational efficiency and smarter resource management. Fluentis acts as the “heart” of the company, managing business activities such as resource planning, order management, inventory, accounting, and more.
Industry 4.0 enables real-time data collection and analysis from devices, sensors, and machinery, improving visibility and automation of production processes. These insights can be integrated into Fluentis, enabling more accurate and timely planning, reducing machine downtime, and optimizing production flow.
The connection between Fluentis and Industry 4.0 machines also enhances transparency across the entire supply chain, improving collaboration with suppliers and customers. This allows companies to respond more quickly to market demands and better manage stock levels.
AI-driven technologies in Industry 4.0 improve predictive maintenance, enabling proactive interventions and minimizing unexpected downtime. Fluentis can be integrated with these systems to automatically manage maintenance tasks and optimize spare parts inventory.
The integration also facilitates customized production to meet specific customer needs. Real-time data analysis made possible by Industry 4.0 allows Fluentis to provide more accurate and immediate reports and dashboards, helping executives make more informed and strategic decisions.
Additionally, the connection between Fluentis and Industry 4.0 machines enhances product quality management. Fluentis can track production data, enabling quick identification of defects or anomalies in the production process.
In conclusion, the connection between Fluentis and Industry 4.0 machines offers significant opportunities to improve efficiency, agility, and competitiveness in manufacturing. Integrating these technologies enables smarter resource management, more flexible and customized production, and better analysis and utilization of business data. Fluentis supports integration through various tools like Bizlink, Frontier Database, or WebAPI.
Customer/Supplier Scoring
Integrated within Fluentis, you’ll find statistics related to supplier scoring. The supply chain is critical for managing components on a Just-In-Time basis. Monitoring delivery punctuality and taking timely action helps the company anticipate potential line stoppage issues.
It is equally important to track your own delivery times. Fluentis includes a statistic on delivery punctuality, allowing you to monitor this metric over a specified time period.
EDI
Fluentis is integrated with the organization that defines the standard format for price lists of companies producing or distributing electrical materials. Fluentis provides real-time visibility of the entire manufacturer’s catalog, highlighting the product codes used in the ERP system, including prices, technical specifications, and barcodes. This is useful for the technical department to find the appropriate component for creating quotes and prototypes. The Fluentis solution allows for the creation or update of products and manufacturer price lists.
External Assembly/On-Site Assembly
With Fluentis, it is possible to manage the assembly and commissioning of specific electrical systems and panels at the job site, including on-site operations. Fluentis allows you to manage individual customer projects with a preliminary bill of materials for the on-site assembly, which differs from the internal production bill of materials. This enables the planning of material procurement for external interventions, resource and personnel scheduling, and management of travel documents and business trips, while also tracking expenses and interventions.
Integration with Automated Warehouses
Fluentis and vertical warehouses are two key elements that, when integrated, can revolutionize business operations’ efficiency and organization.
Vertical warehouses are automated storage systems that leverage vertical space to optimize the storage and retrieval of goods. These systems consist of vertical shelving units that allow quick, automated access to items, reducing picking and packaging times.
The integration of Fluentis with vertical warehouses enables more accurate inventory management, with real-time updates on stock levels and item locations. This optimization of material flow helps minimize human error and improves overall warehouse efficiency.
Learn more
The automation of vertical warehouses enables faster and more accurate picking, put-away, and order preparation, improving customer satisfaction and reducing operational costs.
Fluentis can intelligently plan the put-away of items within vertical warehouses, optimizing space and reducing the time spent searching for products.
Additionally, the integration between Fluentis and vertical warehouses simplifies the management of returns and exchanges, allowing for immediate registration and faster processing of requests. Data generated by vertical warehouses can be synchronized with Fluentis, providing better performance analysis and greater visibility into stock management.
The interface between the two systems supports traceability, allowing easy identification of the origin and path of products within the warehouse and throughout the supply chain.
Moreover, the use of barcodes simplifies the identification and tracking of items, enhancing warehouse operational efficiency. The automation of vertical warehouses reduces the need for manual labor, allowing human resources to be redirected to more strategic, value-added tasks.
In summary, the integration of Fluentis with vertical warehouses enables more efficient, accurate, and automated management of items within storage facilities, improving operational efficiency, customer satisfaction, and overall business competitiveness. Fluentis can connect with these systems through various tools, including Bizlink, Edge Database, or WebAPI.
Prototype Management and Approval Workflows
Managing prototypes in Fluentis is a key process for companies involved in the development and production of new products.
Through prototype management, Fluentis enables companies to organize and track every stage of the prototype lifecycle, from initial conception to final realization. This process provides greater visibility and control over the development of new products, fostering collaboration between design, engineering, and production teams.
Learn more
Fluentis can track materials, phases, costs, markups, and resources used for each prototype, enabling accurate evaluation of development and production costs, as well as the final sale price.
Additionally, managing prototypes in Fluentis helps identify and address any issues or delays in development, improving efficiency and reducing time to market.
Fluentis allows companies to document and store all data related to prototypes, including drawings, costs, prices, specifications, and test results, making it easy to retrieve information in the future. The integration of prototype management with other Fluentis features, such as quote management, order processing, and inventory control, enables better forecasting of material and resource needs for mass production.
Thanks to the automation provided by Fluentis, prototype approval and authorization processes can be simplified, speeding up development.
Fluentis promotes standardization of development processes, allowing companies to adopt consistent methodologies and best practices. Centralized access to prototype information within Fluentis improves communication across departments, enabling prototypes to be directly included in sales quotes.
The integration between Fluentis and design and simulation tools allows direct linking of data and information on prototypes, streamlining the decision-making process. Fluentis also helps manage the lifecycle of prototypes after market launch, tracking any modifications or updates made over time.
Prototype management in Fluentis enhances traceability and compliance with regulations, particularly for companies operating in regulated industries. The system’s data storage ensures the protection of intellectual property and sensitive information.
In conclusion, prototype management in Fluentis offers an integrated and comprehensive platform to coordinate and optimize the entire new product development process. Through automation, data integration, and traceability, companies can gain significant advantages in efficiency, collaboration, and control.
Fluentis automates prototype management completely. A client quote can be quickly generated by specifying the work cycle, bill of materials (BOM), and any additional costs. The quote, processed through an approval workflow, is sent via email to the client, who can accept it directly from their inbox. This input automatically generates the cycle and BOM, enabling immediate production initiation.
Discover how Fluentis ERP
can transform your business
15-day free trial | No automatic renewal | Instant access
Contact us for more information
Get in touch with us if you:
- Are a SME in Manufacturing, Distribution, or Services
- Need to streamline and digitalize your business processes
- Want to take advantage of the benefits of a native cloud solution
- Want to replace your non-integrated softwares with a unified ERP platform
+1 281 404 1726
Chat with us