ERP Software for the Doors and Windows Industry
Fill out the form to request information
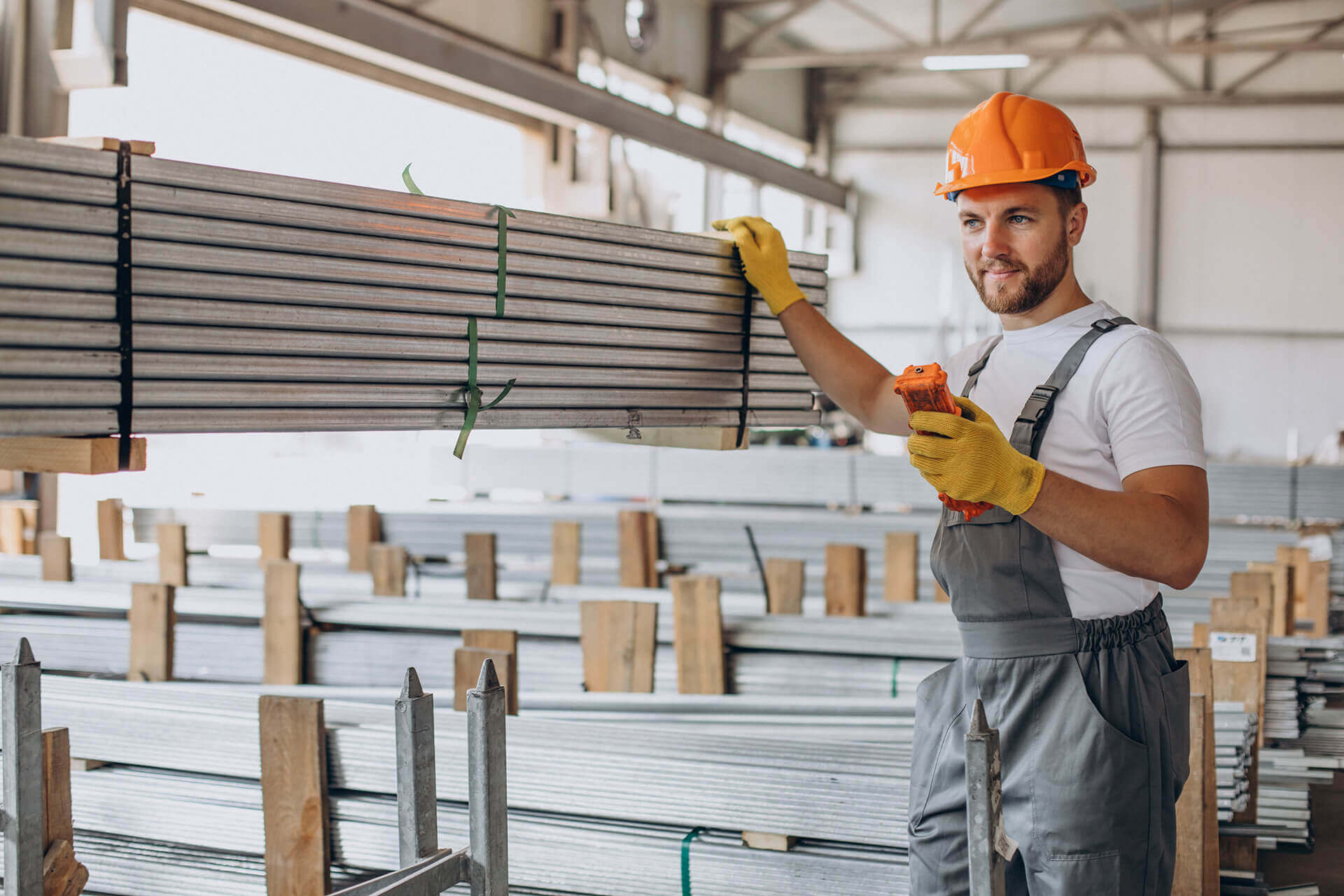
A Tailored ERP for the Doors and Windows Industry
Fluentis ERP offers a specialized management solution for companies manufacturing doors, windows, and armored doors. This solution includes features and algorithms designed to handle all internal and external business processes across the entire product lifecycle. From product configuration to sales, material procurement, internal and subcontracted production scheduling, production data collection, and Industry 4.0 connectivity for production systems and automated warehouses, Fluentis ERP delivers a comprehensive toolset for the industry.
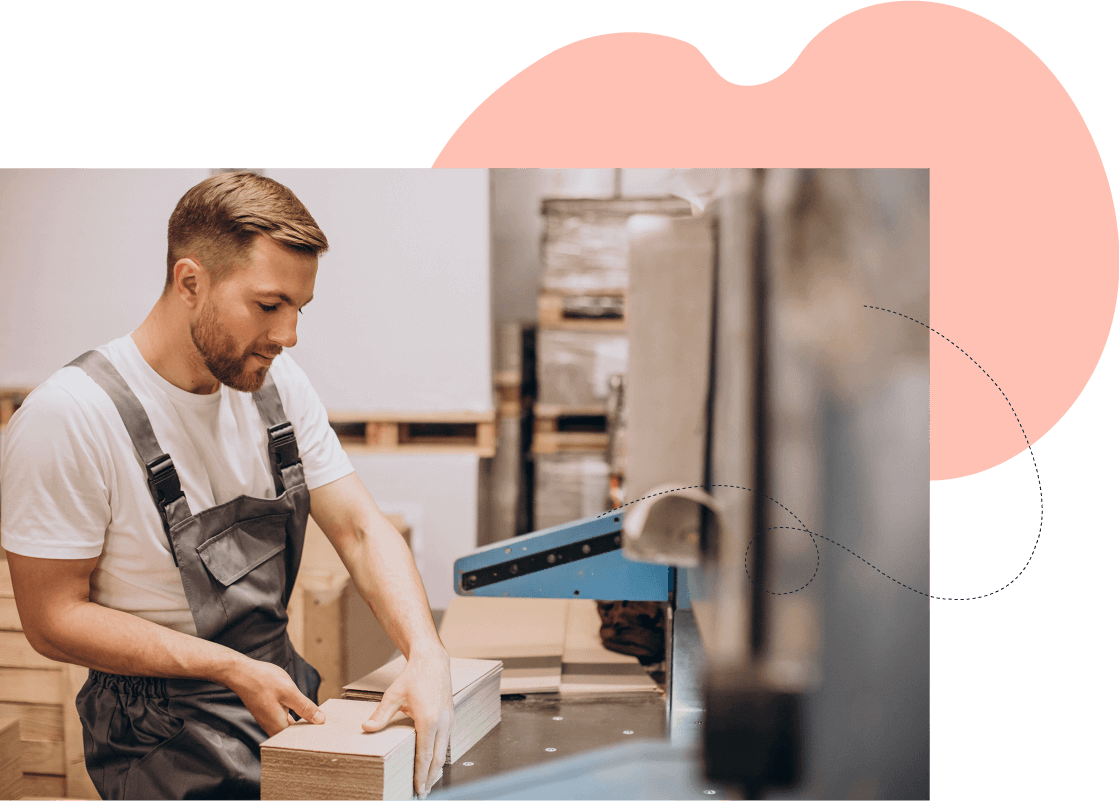
Boost Your Performance with Fluentis ERP
Fluentis ERP for Doors and Windows is a powerful tool for enhancing competitiveness by enabling full integration across the entire supply chain. With automated information sharing between all stakeholders—including end customers, suppliers, and subcontractors—Fluentis ensures seamless collaboration.
The solution includes dedicated apps that streamline subcontractor management, providing real-time updates on commissioned work and progress tracking. Fluentis also integrates business growth tools like CRM and B2B/B2C e-commerce platforms, all feeding into a comprehensive management control system tied to Finance and Treasury operations.
This integration boosts flexibility and service quality—critical factors for the success of door, window, and frame manufacturers—equipping them to navigate the challenges of an ever-changing market.
Additionally, Fluentis ERP comes with integrated add-ons such as Business Analytics, featuring dashboards to monitor key business KPIs, and a WMS module. The WMS operates via a touch-based RF application, handling material flows from goods receipt through internal logistics to final shipment, ensuring efficiency and precision at every stage.
Are you in this industry and facing a specific challenge that's impacting your efficiency?
See what we can do for you
Send us your RequestStrengths of Fluentis ERP for Door and Window Manufacturing:
Product Configurator
Management of Multi-Level Parametric BOMs
Procurement Policy Management
Phase Grouping / Work Order Batch Management
MES with Time Tracking, Progress Monitoring, and Label Printing
Industry 4.0 Integration
Nesting and Cutting Plan Management, Optimizers, and Integration with Specific Software
Shipping Plan Management, Picking, UDC, WMS
Product Sheet
CE Labeling
Finished Product Traceability
Routine and Emergency Maintenance (Support)
Non-Conformance Management
Defective Product Return
Integration with Automated Warehouses
Product Configurator
The Fluentis Product Configurator is a powerful technical and commercial tool that allows for dynamic management of items, pricing, and BOMs without requiring prior component codification.
The Fluentis Configurator applies technical and commercial models and rules, transforming configuration options—such as dimensions, color, or door swing direction—into accurate BOMs, production workflows, and calculated product sales prices.
Designed for ease of use, it guides users through the product option selection process while ensuring compliance with predefined parameters, rules, constraints, and commercial guidelines. This ensures accuracy, efficiency, and consistency in product configuration and pricing.
Management of Multi-Level Parametric BOMs
The management of multi-level parametric BOMs in Fluentis allows for the use of formulas to calculate dimensions and material usage coefficients for semi-finished goods and raw materials, inheriting parameters from higher levels.
This functionality enables the use of template BOMs without requiring the creation of new BOMs for every dimensional variation.
Procurement Policy Management
Fluentis includes an integrated system for managing various procurement policies for semi-finished goods and raw materials, supporting strategies such as Make-to-Order (MTO), Make-to-Stock (MTS), and Assemble-to-Order (ATO).
This system leverages historical consumption data and forecasts derived from MPS production plans or sales forecast explosions (demand forecasting). By doing so, it minimizes stockouts and optimizes inventory levels.
Phase Grouping / Work Order Batch Management
In production sectors where processes are often fast-paced, planning is job-driven, and production optimization criteria can vary between operations, grouping tasks or cycles with similar characteristics becomes essential. For instance, processes might be grouped by profile section during milling, independent of the product’s final finish.
Work order batches in Fluentis enable the grouping of multiple phases across different orders, provided they share the same work center. Operators can log setup times, production times, quantities produced, and non-conforming items directly to the batch. The system then automatically distributes these metrics across the appropriate phases and work orders.
MES with Time Tracking, Progress Monitoring, and Label Printing
The Manufacturing Execution System (MES) is designed to be used directly on the shop floor by operators at the machine.
Its user-friendly, wide-screen interface ensures smooth operation on traditional PCs, touch monitors, or tablet PCs.
Learn more
This system integrates in real-time with Fluentis ERP, allowing operators to:
- Verify production sequences
- Access production documentation
- Record machine downtime and cycle times
- Declare quantities of conforming or non-conforming products
- Record process quality checks
- Monitor production KPIs, progress tracking, and OEE (Overall Equipment Effectiveness)
- Print product identification labels
Learn more about Fluentis integrated MES
Industry 4.0 Integration
The integration between Fluentis and Industry 4.0 machines is a key element for optimizing and digitally transforming industries. Industry 4.0 is characterized by the incorporation of digital technologies into manufacturing processes.
Thanks to the connection between Fluentis and Industry 4.0 machines, companies can achieve greater operational efficiency and smarter resource management. Fluentis serves as the “core” of the business, managing essential activities such as resource planning, order management, inventory, and accounting.
Learn more
Industry 4.0 allows for real-time data collection and analysis from devices, sensors, and machines, improving visibility and automating production processes. This data can be integrated into Fluentis, enabling more accurate and timely planning, reducing machine downtime, and optimizing production flow.
The integration between Fluentis and Industry 4.0 machines enhances transparency across the entire supply chain, improving collaboration with suppliers and customers. This leads to better responsiveness to market demands and more efficient stock management.
The use of AI within Industry 4.0 can improve predictive maintenance, enabling proactive interventions and reducing unplanned downtime. Fluentis can integrate with these systems to automatically manage maintenance operations and optimize spare parts inventory.
Moreover, the connection between Fluentis and Industry 4.0 machines facilitates customized production and the personalization of products to meet specific customer needs. Real-time data analysis, made possible by Industry 4.0, enables Fluentis to provide more accurate and immediate reports and dashboards, helping managers make more informed and strategic decisions.
Additionally, this integration ensures better product quality management. Fluentis can track production data, allowing for the quick identification of defects or anomalies in the production process.
In conclusion, the connection between Fluentis and Industry 4.0 machines offers significant opportunities to improve efficiency, agility, and competitiveness in manufacturing. Integrating these technologies enables smarter resource management, more flexible and customized production, and enhanced data analysis and utilization. In Fluentis, integration can be achieved through various tools such as Bizlink, frontier databases, or WebAPI.
Nesting and Cutting Plan Management, Optimizers, and Integration with Specific Software
Data exchange with cutting optimization software allows for the sending of material requirements to be optimized and the receipt of output with optimized quantities and work sequences. Production progress can then be managed based on nesting codes or cutting jobs, which will be handled as work orders.
Shipping Plan Management, Picking, UDC, WMS
The shipping phase is managed by organizing shipments into load plans that can be scheduled, providing visibility into the weight and volume of the materials to be sent to customers. The picking phase is managed using WMS software with mobile terminals that guide operators through warehouse locations. Operators confirm picking tasks for load units (UDCs) by scanning the barcode on each package, and this information is made available in real-time within Fluentis ERP.
Product Sheet
Fluentis allows for the creation and revision of technical datasheets, specifically the “Declaration of Performance” (DoP) in compliance with the performance requirements outlined by applicable CE marking regulations.
CE Labeling
It is possible to create production and/or packaging labels for products, ensuring compliance with the requirements of UNI EN 14351, including the mandatory CE information and the manufacturer’s details.
Finished Product Traceability
Fluentis ensures the traceability of the entire production chain using lot numbers for raw materials and semi-finished goods. For finished products, it allows for the use of production lots as well as assigning a serial number or identification number to each produced item (such as for fire-resistant doors).
Routine and Emergency Maintenance (Support)
Fluentis enables the creation and reporting of maintenance services (both routine and emergency) on products provided, based on customer requests.
Non-Conformance Management
In accordance with technical regulations and referring to UNI EN ISO 9001 standards, Fluentis allows the registration and management of non-conformance flows during procurement or production. This includes defining responsibilities, actions taken to resolve the identified issue, tracking deadlines, activities assigned to responsible parties, and associated costs.
Defective Product Return
As per technical regulations and in reference to UNI EN ISO 9001 standards, Fluentis allows the registration and management of customer complaints (commercial or technical) in the post-sale or installation phase. This includes defining responsibilities, approval of return/replacement requests, actions taken to resolve the issue, and monitoring deadlines and activities assigned to responsible personnel, as well as tracking associated costs.
Integration with Automated Warehouses
Fluentis and vertical warehouses are two key elements that, when integrated, can revolutionize the efficiency and organization of business operations.
Vertical warehouses are automated storage systems that make use of vertical space to optimize the storage and retrieval of goods. They consist of vertical shelving units that allow for quick and automated access to items, reducing picking and packaging times. The integration between Fluentis and vertical warehouses enables more accurate inventory management, with real-time updates on stock levels and item locations, optimizing material flow and minimizing the risk of human error.
Learn more
Automating vertical warehouses increases speed and accuracy in picking, storing, and order preparation, enhancing customer satisfaction while reducing operational costs.
Fluentis can intelligently plan the placement of items within vertical warehouses, optimizing space and reducing the time spent searching for products.
Additionally, the integration between Fluentis and vertical warehouses simplifies the management of returns, allowing for immediate registration and faster processing of requests. Data generated by vertical warehouses can be synchronized with Fluentis, enabling better performance analysis and greater visibility into stock management.
The interfacing between the two systems also facilitates product traceability, allowing easy identification of the origin and movement of goods within the warehouse and across the entire supply chain.
Using barcodes further simplifies the identification and tracking of items, improving warehouse operation efficiency.
Automating vertical warehouses reduces the need for manual labor, freeing up human resources to focus on more strategic and value-added tasks.
In summary, the integration between Fluentis and vertical warehouses allows for more efficient, accurate, and automated management of items within storage facilities, improving operational efficiency, customer satisfaction, and overall business competitiveness. In Fluentis, the interconnection can be achieved using various tools: Bizlink, Frontier Database, or via WebAPI.
See What Our Customers Say
No references available
Discover how Fluentis ERP
can transform your business
15-day free trial | No automatic renewal | Instant access
Contact us for more information
Get in touch with us if you:
- Are a SME in Manufacturing, Distribution, or Services
- Need to streamline and digitalize your business processes
- Want to take advantage of the benefits of a native cloud solution
- Want to replace your non-integrated softwares with a unified ERP platform
+1 281 404 1726
Chat with us