ERP Solutions
for Custom Manufacturing
Fill out the form to request information
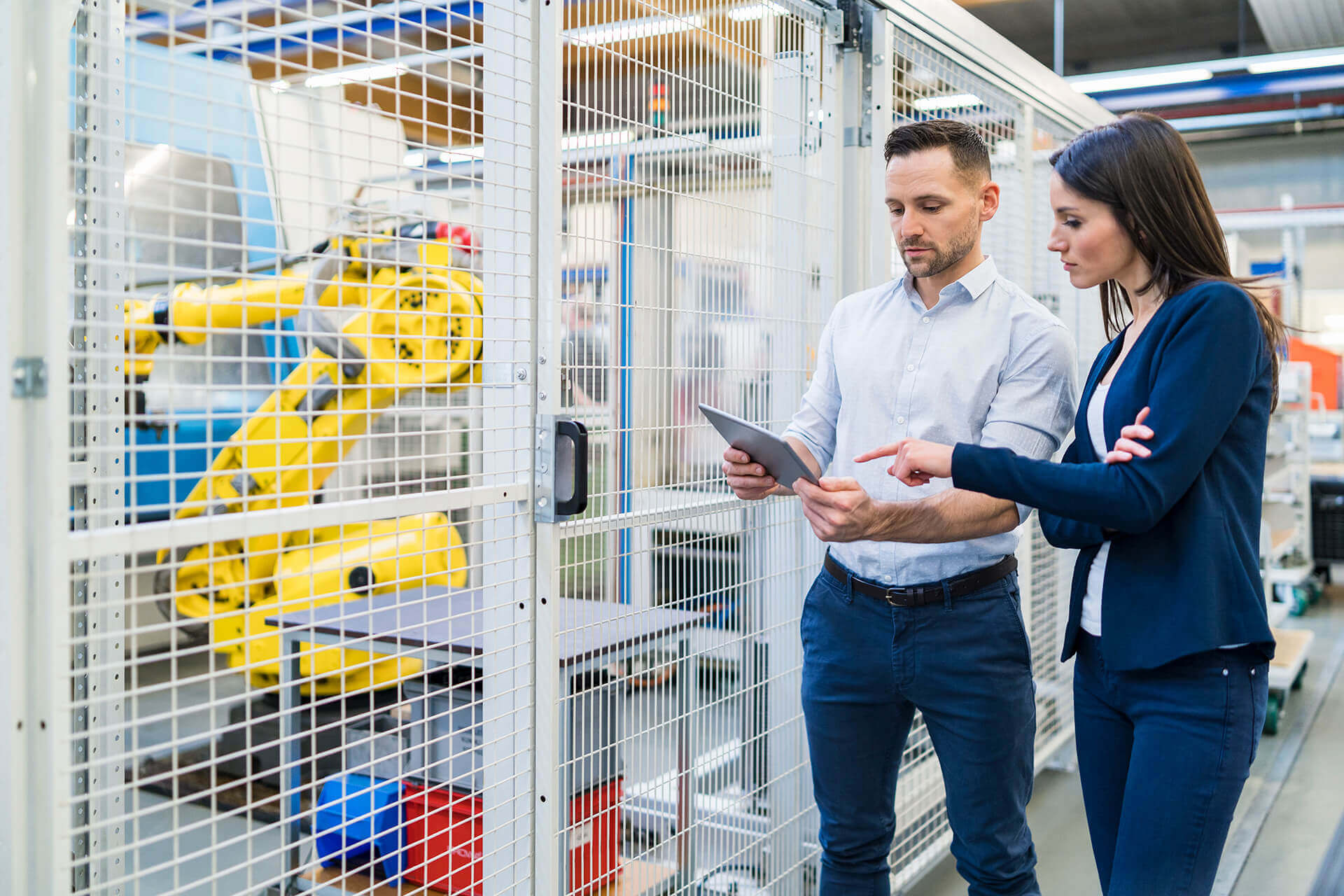
Optimize Custom Manufacturing with Fluentis ERP
Fluentis ERP provides a powerful, easy-to-use solution designed for manufacturing and engineering companies that rely on custom, project-based production, including Engineering To Order (ETO) strategies.
With Fluentis ERP, you can connect all your business processes for smooth project management at every stage: quoting, design, production scheduling, material and resource planning, logistics, both in-house and outsourced production, cost control, and financial planning.
Easily manage cost estimates and final accounting to boost project margins. Plan and schedule production efficiently to increase productivity and ensure on-time delivery.
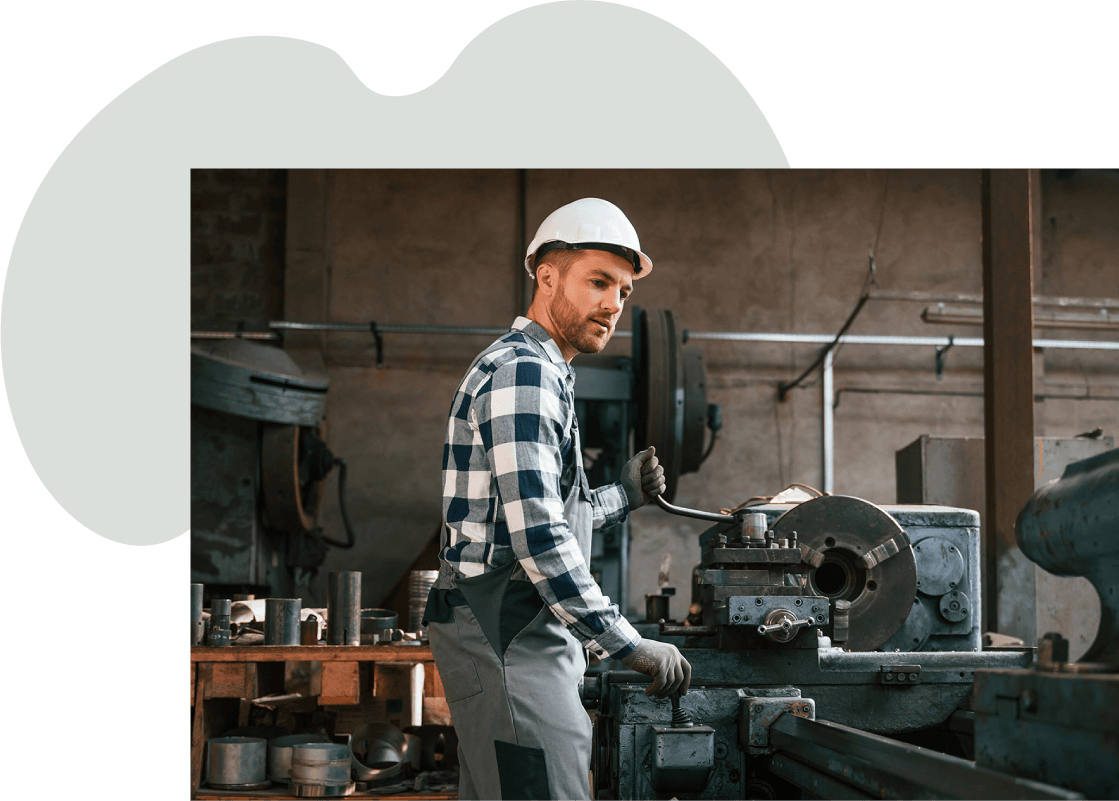
Fluentis has developed an ERP software solution specifically for Engineering to Order (ETO) custom manufacturing, featuring tools and algorithms designed to manage every internal and external business process throughout the entire product lifecycle. From Project Management and Sales to material procurement, production Scheduling (in-house or subcontracted), and real-time Production Data Collection, Fluentis ERP covers it all. Additionally, the solution integrates Industry 4.0 capabilities to seamlessly connect Production equipment and Automated Warehouses.
Key Aspects of Project-Based Manufacturing
Project-based manufacturing is becoming increasingly significant in today’s fast-paced market, where speed and flexibility are essential. Companies that operate in this model can deliver unique, highly customized products that require effective solutions for managing costs, revenue, and schedules.
This type of production allows companies to meet customer and market demands by tightly aligning design and production workflows. As a result, the customer is a key part of the entire production process—from the initial design phase, where technical specifications are defined, to procurement, production, and the final delivery of the product.
During these key phases, companies often face challenges that can be summarized as:
Creating accurate estimates
Ensuring on-time delivery
Tracking costs and profitability
Are you in the Custom-Manufacturing Industry and facing a specific challenge that's impacting your efficiency?
See what we can do for you
Send us your Request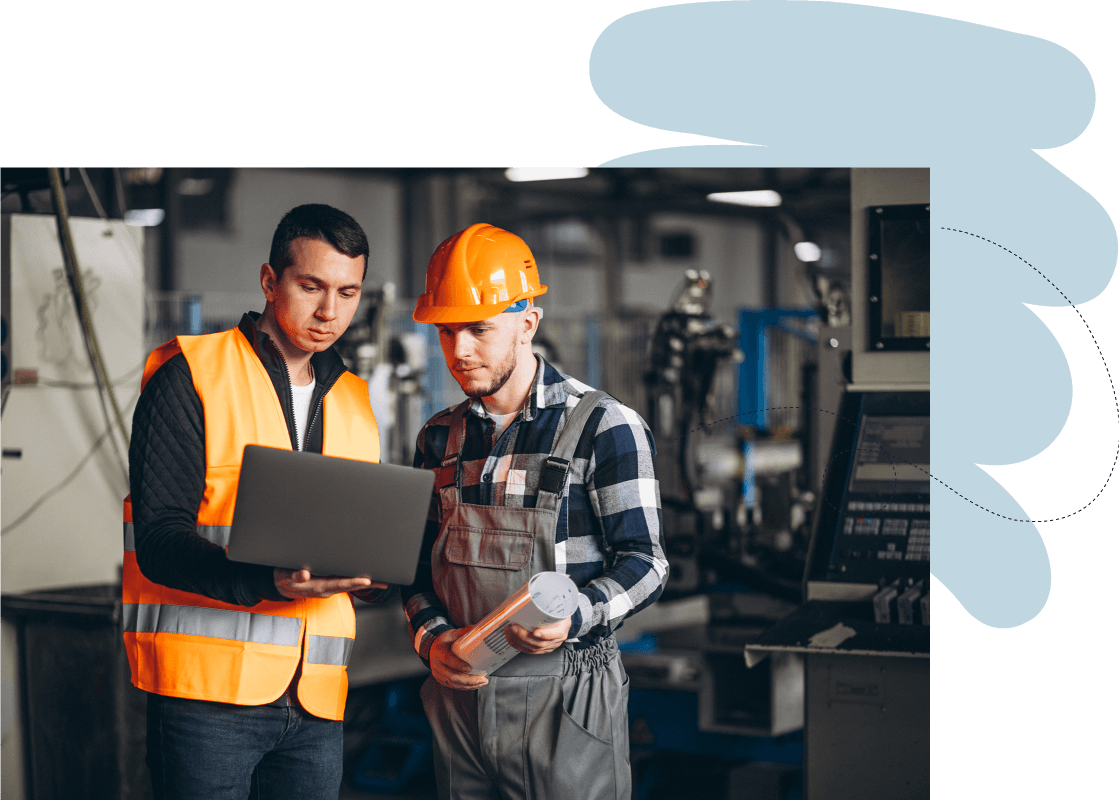
An ERP Solution for Project-Based Manufacturing
Having the right tools to manage and optimize production is crucial to maintaining competitiveness in today’s market.
Many companies still rely on manual methods for project planning, which often results in inefficiencies, inaccurate outcomes, errors, and delays in on-time delivery. Implementing an ERP system specifically designed for project-based manufacturing can bring significant benefits, as it integrates all the key processes involved—estimating, design, planning and scheduling, order management, and cost and margin control.
Fluentis ERP, in particular, addresses three core challenges commonly faced by project-based manufacturers: generating accurate quotes, ensuring on-time delivery, and monitoring costs and profitability.
Establishing Realistic Estimates
It all starts in the quoting/prototyping phase, which is the initial stage where cost and revenue estimates are made for the proposal. From here, several workflows are triggered that involve operational, technical, and sales teams. During this phase, businesses may face challenges that, if not successfully addressed, could jeopardize the entire project organization.
Common challenges include accurately assessing costs and revenues, appropriately valuing technical interventions or markups, and ensuring access to and modification of historical data, which should then be shared with all stakeholders involved in the project.
A Unified Data System
With Fluentis ERP, all departments operate on a single, centralized database. Each user, based on their access rights, can contribute to creating the estimate. Through the Prototype Management module, users can either create a new prototype starting from pre-existing standardized products by importing the bill of materials (BOM), or they can develop an entirely new prototype that is only coded once the client approves it.
The Prototype Management tool simulates all costs and revenues for the potential production batch being quoted. With just a few clicks, users can view both the costs—based on recent, average, or standard material costs in the BOM, labor costs for specific tasks, and any overhead costs like electricity or depreciation—and the associated revenues, applying a markup either as a percentage or a fixed value.
Once the estimate is created, it is included in a sales proposal, which can go through various stages of review. Once confirmed, it automatically converts into a customer order.
Documents Under Control
With Fluentis ERP, all documents are consistently tracked and linked, enabling easy access to historical estimates and allowing for the application of appropriate markups. Say goodbye to spreadsheets—Fluentis ERP integrates these processes directly into the system, ensuring continuous cost control.
Ensuring On-Time Delivery
Many project-based manufacturers intend to use their ERP system for production planning but often only partially rely on it. They start with the ERP to outline production, then move outside the system to tools like Excel and Microsoft Project.
This fragmented approach introduces risks, as it provides visibility into only a portion of the data required for effective planning, and the data isn’t integrated with the ERP or synchronized across departments. This lack of alignment makes it challenging to keep key departments—such as engineering, sales, procurement, and production—coordinated, which is essential for maintaining on-time delivery.
Limited visibility into supply chain and production data can lead to issues such as material shortages, machine downtime, and unexpected delays, resulting in missed delivery deadlines and increased costs.
All Data in a Single Database
Fluentis ERP offers specialized Planning and Scheduling tools, providing constant access to all necessary data within a single, centralized database. With Fluentis, companies can generate and schedule single-product or multi-product orders based on their specific needs. From a production order, users can seamlessly release purchase, subcontracting, or production work orders, maintaining document traceability and visibility across the entire supply chain to ensure timely delivery.
The subcontracting module in Fluentis supports both phase-based and full subcontracting (including code changes).
APS Solution
Fluentis ERP offers an Advanced Planning System (APS) designed to optimize project-based manufacturing. This fully integrated system supports Production Planning and Scheduling with advanced algorithms that simulate factory operations, identifying and resolving potential issues in advance. The algorithm factors in stock levels, availability, and actual usability by adjusting for items that are “unavailable” or located in “non-usable” locations.
Key APS functionalities in Fluentis ERP include:
- Real-time job scheduling for reliable, on-time delivery with clear visibility into work center capacity.
- Maximizing resource efficiency by balancing workloads to maintain high utilization levels.
- Synchronizing production with purchasing to prevent material shortages and balance inventory with production needs.
- Anticipating critical materials and bottlenecks.
- Reducing production lead times.
- Managing low stock, alternative items, and alternate phases.
- Minimizing manual intervention through histograms that display capacity and order priority.
- Ensuring KPI adherence for performance goals.
Monitoring Costs and Margins
Using ERP systems to track production orders, both in terms of cost and performance, enables companies to understand the margin on each job and maintain a real-time view of the business’s financial health.
With the data provided by the system, companies can quickly pinpoint any necessary corrective actions, reducing response times and improving overall efficiency.
Job Costing
Fluentis ERP simplifies tracking production job status through its Job Costing feature, providing clear insights for both single-product and multi-product orders. This functionality enables detailed cost breakdowns by comparing actual materials used against the planned Bill of Materials (BOM).
Two types of costs are calculated: estimated costs, based on BOM component totals, with the option to value at average, last, standard, or list price; and actual costs, derived from purchase orders, subcontracting, or production records.
Fluentis ERP integrates and simplifies all processes in project-based manufacturing
Quoting/Prototyping
Specific Features:
- Creation of a manual quote/prototype, from template, from Bill of Materials, or using a configurator.
- Bulk editing of components within various prototypes.
- Prototype cost recalculation based on the latest average, last purchase, or standard material costs.
- Archiving of documents related to the prototype and associated quote.
- Management of versions and commercial status of the quote/offer.
- Display of quotes in progress, closed, or canceled.
- Comparison between initial quote and actual job costing once in production.
Project Design
Specific Features:
- CAD Integration with tools like Solid Edge, CATIA, etc., using approval workflows for drawing revisions, technical specifications, and project confirmations.
- Integration with Project Management Module to support scheduling and activity reporting.
- Document Management allowing technical specifications, drawings, control plans, etc., to be attached within the project.
- Resource Assignment to specific project Work Packages (Planner for schedule management synced with Outlook calendars).
- Creation and Management of Purchase Requisitions (PRs) directly from the project within the Project Management module.
- Real-Time Monitoring of project status based on declared project activities.
- RFQ Management for streamlined procurement requests.
Administration
Specific Features:
- Creation and modification of accounting entries
- Viewing, opening, and closing accounts
- Currency adjustments and year-end journal entries
- Management of VAT movements, VAT protocols, annual VAT communications, periodic VAT settlements, and VAT payments
- Electronic invoicing with non-resident entities / VAT reporting
- Management of VAT limits (Plafond)
- Management of VAT Reports (Spesometro)
- Intrastat reporting and related forms
- Management of loans, accounts payable/receivable, payments, collections, commissions, and reminders
- Interest management and internal transfers (giroconti)
- Commission calculations, F24 forms, Enasarco management, and withholding certificates
- Asset management, depreciation, and related accounting entries
- Management of leasing and maximum lease payments (maxicanone)
- Management of SDI documentation: incoming purchase documents, outgoing sales invoices, outgoing VAT communications, and international documents
Business Processes
Specific Features:
- Management and analysis of cash flow and off-balance sheet due dates.
- Management of advance invoices (down payments).
- Creation of promissory notes, overdue payments, and management of telematics files for RiBA (Bank Collection) and SDD (Direct Debit).
- Payment management, accounts payable, and bank account reconciliation.
- Use of credit lines, risk and exposure calculation for customers, average payment currency calculation, and lock management.
- Integration with DocFinance and Piteco.
Management Control
Specific Features:
- Closing of interim accounts, non-accounting entries, consolidation, integration, and adjustment entries.
- Management of analytical accounting and budgeting entries.
- Use of reclassification models and related comparisons.
- Management of sales forecasts, market, and product centers.
- Recalculation of costs and yields.
- Ability to value assemblies.
- Product cost calculation, project reporting.
Sales and Project Management
Specific Features:
- Automatic conversion of quotes into orders once confirmed, including approval workflows.
- Creation of supplier orders from sales orders.
- Details on sales terms, credit limits, cash flow, and delivery dates.
- Linkage within the order to technical projects and specific work units.
- Integration with the CRM module for managing potential customers and opportunities.
- Direct import of quotes from CRM contacts.
- Conversion of CRM contacts into customers when the order is confirmed.
- Multilingual document management.
- Automatic order fulfillment in delivery notes (DDT).
- Automated email notifications for order confirmations with attachments.
- Visualization of the project status once the order is released for production.
- Management of agents and commissions per agent.
- Management of billing schedules with proposed billing dates.
- Management of the accounts receivable schedule.
- Management of a project with hierarchical structure (WBS) or by order.
- Import of WBS project structure into an order.
- Management of project milestones.
- Automatic generation of production orders.
Project Management
For some clients, the concept of a “job” (or “order”) extends beyond production and also covers post-sales activities, or even spans across all business functions. Fluentis is designed to manage this broader view of “job” or “order.”
In the Project Management module, Fluentis supports tracking the various components of a project/order through Work Breakdown Structure (WBS) nodes at multiple levels.
This enables us to handle all aspects of external project planning. We can plan, monitor, and track external tasks and resources using various devices (smartphones, tablets, or PCs).
Production Planning
Some specific features:
- Finite and infinite capacity scheduling.
- Customizable alerts to track changes to bills of materials or work cycles.
- Analysis of item availability.
- Release of planned orders based on job priorities.
- Material planning and resource scheduling with both finite and infinite capacity.
- Project resource planning through a Planner and calendars managed by a Project Manager.
- Production simulations.
- Verification and analysis of work centers.
APS Scheduling
Some specific features:
- Definition of the Master Production Schedule (MPS).
- Definition of single-product or multi-product work orders.
- Work order costing for real-time tracking of costs and revenues.
- Finite and infinite capacity scheduling.
- Planning by work order and priority.
- Visibility of production capacity by work center.
- Ability to simulate work orders and view them using a Gantt chart.
- Material requirements planning (MRP) execution.
- Automatic generation of production, subcontracting, and purchase orders for seamless integration with the Supply Chain.
- Analysis of bill of materials (BOM) requirements for assemblies.
- Real-time availability analysis of materials.
Maintenance and Support
Some specific features:
- Management of resources and scheduling of internal or external interventions through project WBS (Work Breakdown Structure).
- Declaration of interventions with invoicing and management of project costs and final reporting.
Procurement
Some specific features:
- Management of Requests for Quotation (RFQ) and Purchase Requests (PR).
- Automatic generation of supplier orders from PR or RFQ, or from Customer Orders.
- Goods receipt and creation of Purchase Delivery Note (DDT).
- Automatic generation of purchase invoices from receipts or DDT.
Logistics
Some specific features:
- Warehouse management with the ability to manage by location.
- Location management.
- Management of batch and serial number records.
- Advanced picking management using WMS (Warehouse Management System).
- Management of UDC (Unit Load) by order.
- Management of load parameters and daily operations.
Quality
Some specific features:
- Management of technical data sheets with appropriate product revisions.
- Creation and management of control plans.
- Monitoring of items from subcontracting returns, purchases, or production receipts.
- Management and creation of certificates of analysis.
- Management of complaints and non-conformities (NC).
- Handling of corrective actions following complaints or NC.
- Management and creation of personnel certificates.
- Compliance management of standards and regulations.
Discover how Fluentis ERP
can transform your business
15-day free trial | No automatic renewal | Instant access
Contact us for more information
Get in touch with us if you:
- Are a SME in Manufacturing, Distribution, or Services
- Need to streamline and digitalize your business processes
- Want to take advantage of the benefits of a native cloud solution
- Want to replace your non-integrated softwares with a unified ERP platform
+1 281 404 1726
Chat with us