ERP Solutions
for the Automation / Machinery / Equipment Sector
Fill out the form to request information
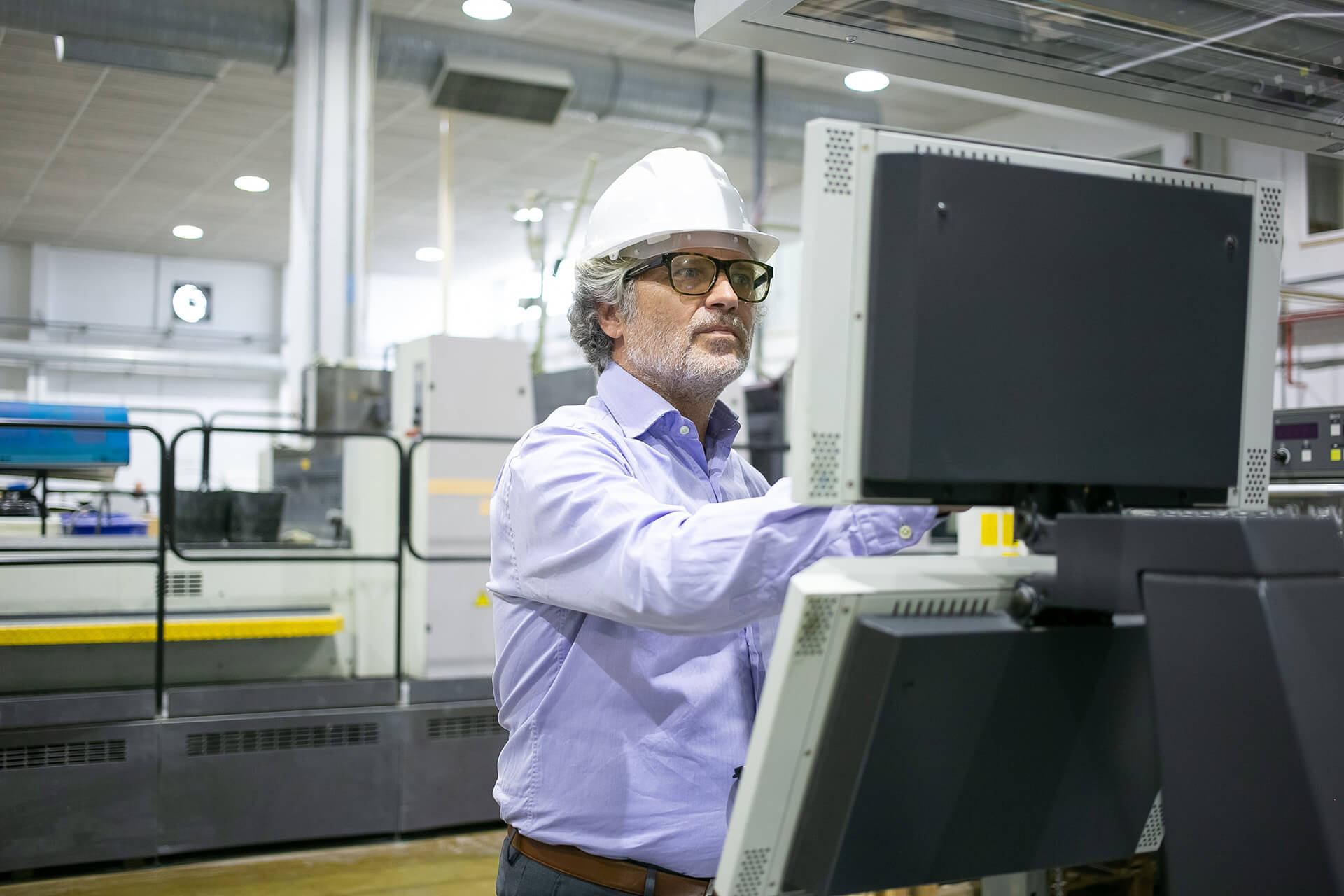
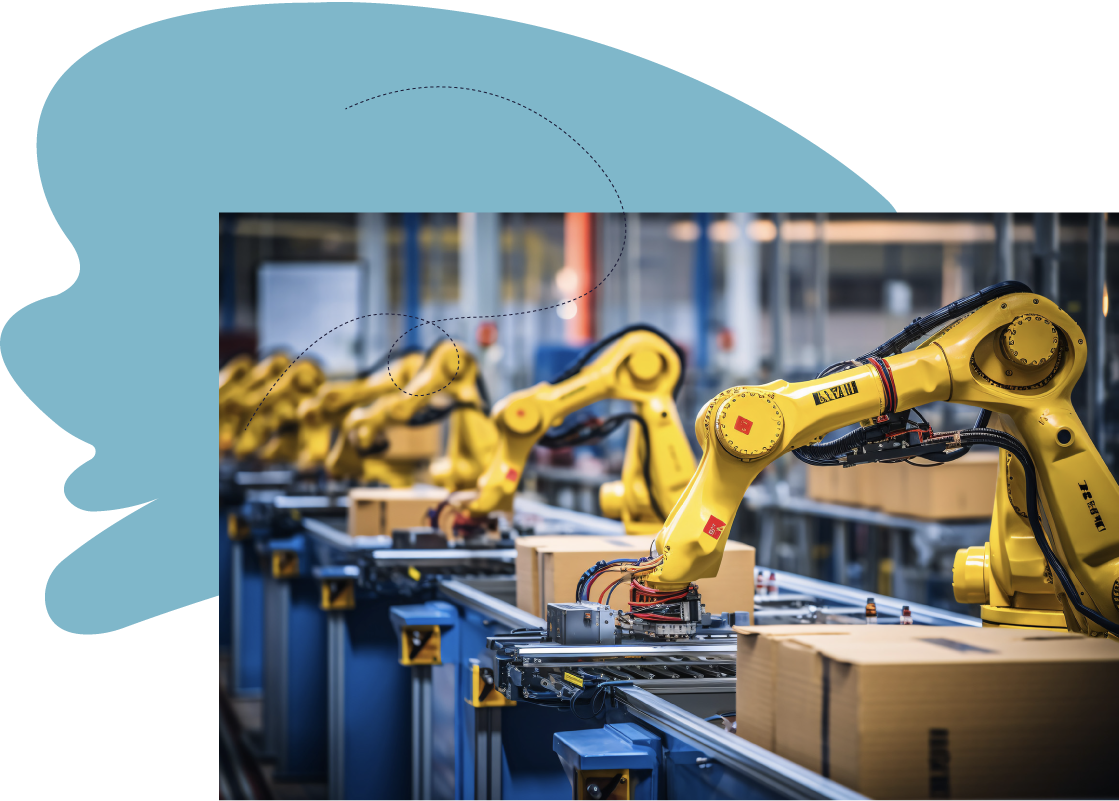
The ERP solution for companies in the Automation / Machinery / Equipment sector
In recent years, companies operating in the Automation, Machinery, and Equipment sector have faced increasingly complex challenges in managing their daily operations. The rising demand for efficiency, precision, and competitiveness has made it essential to adopt advanced business management solutions.
This is where Fluentis comes into play — a powerful ERP system that enhances how companies tackle the sector’s challenges.
Fluentis ERP provides a comprehensive view of business operations, enabling managers to make faster, data-driven decisions. In an industry where complexity is the standard, Fluentis helps automate key processes, improve product traceability, and ensure a seamless workflow.
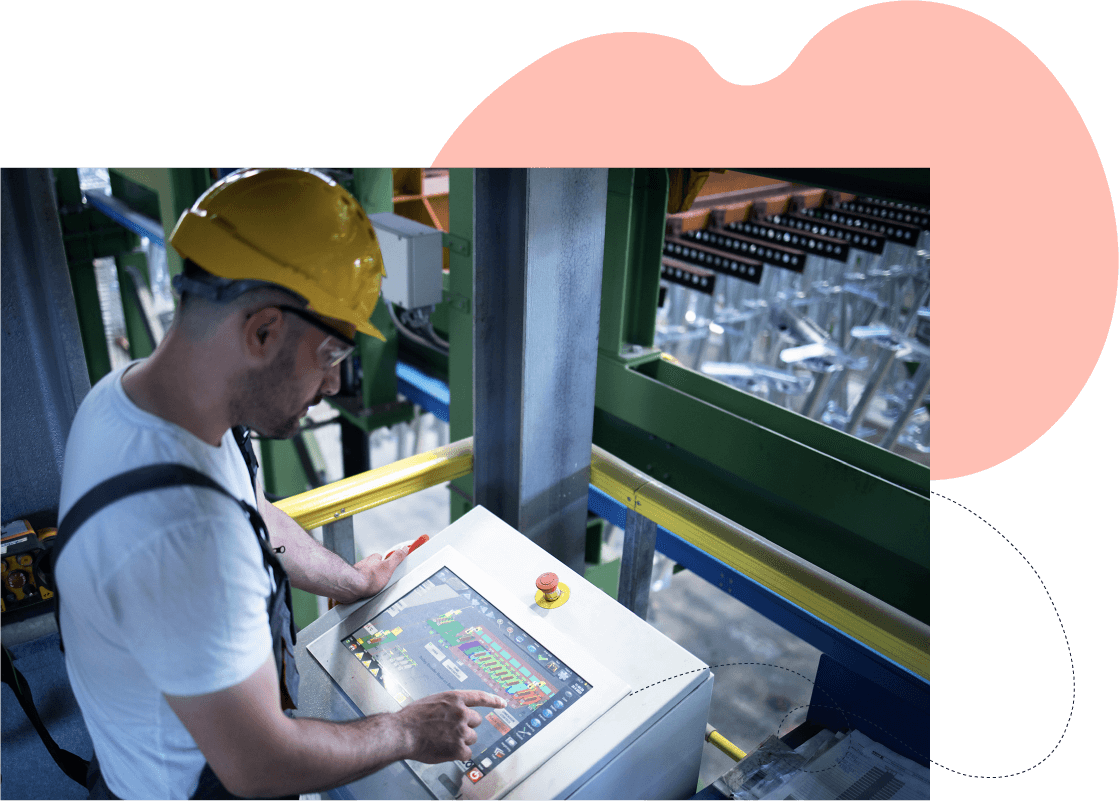
Solution Features
In a constantly evolving world, companies in this sector often face complex and ever-changing challenges.
Businesses operating in the Automation, Machinery, and Equipment sector have unique needs that frequently require a tailored approach. A well-designed ERP system allows for the seamless integration and efficient management of all business processes — from procurement to production, logistics to controlling — ensuring real-time, accurate control over every aspect of the company.
Fluentis provides customized solutions that help businesses quickly adapt to market changes, streamline workflows, and maximize operational efficiency. Additionally, the data collection and analysis generated by the system deliver valuable insights to support informed, strategic decision-making.
Below are the standard Fluentis modules that enhance business management for companies in this sector, alongside core functionalities that benefit all companies, such as Administration, Sales, and Purchasing.
Prototyping
Project
Resource Planning (materials and workforce)
Batch Management
Controlling
WMS
MES
Strengths of Fluentis ERP for the Automation/Machines/Plants Sector
Prototyping
Prototype Management in Fluentis is a fundamental process for companies in the sector.
Through Prototype Management, Fluentis allows companies to organize and track all stages of the lifecycle, from the initial concept to the final realization.
This process provides greater visibility and control over the development of new products, facilitating collaboration between design, engineering, and production teams.
Fluentis can track materials, phases, costs, mark-ups, and resources used for each prototype, enabling an accurate evaluation of development and production costs, as well as the sales price.
Moreover, Prototype Management in Fluentis helps to identify and promptly resolve any issues or delays during development, improving efficiency and reducing time-to-market.
Fluentis allows the documentation and storage of all prototype-related data, including drawings, costs, prices, specifications, and test results, making information easily retrievable in the future. The integration between Prototype Management and other Fluentis features, such as quotes, orders, and inventory management, helps to forecast material and resource requirements for large-scale production.
Thanks to Fluentis automation, approval and authorization processes can be simplified, accelerating prototype development. Prototype Management in Fluentis promotes the standardization of development processes, allowing companies to adopt uniform methodologies and best practices.
Centralized access to prototype information within Fluentis improves communication between departments, making it possible to directly include prototypes within sales offers.
It is also possible to automatically create the Bill of Materials (BOM) and production cycle directly from the selected prototype.
Prototype Management in Fluentis offers an integrated and comprehensive platform to coordinate and optimize the entire new product development process. Through automation, data integration, and traceability, companies can achieve significant improvements in efficiency, collaboration, and control.
Project
Project Management is essential for the success of any modern organization, as it enables the maximization of operational efficiency and profitability.
Project Management within Fluentis creates an ecosystem that allows for more accurate planning, optimal resource allocation, and real-time performance monitoring, as projects are connected to almost all company functions.
Project Management in Fluentis makes it possible to define clear objectives, assign responsibilities, monitor progress, and manage resources efficiently. This results in cost reduction, increased productivity, and greater customer satisfaction.
Moreover, Fluentis provides an overview of all ongoing projects, enabling better resource allocation and priority scaling based on strategic value. This is crucial to ensure that projects are aligned with business objectives.
The integration of Project Management in Fluentis is an essential step to improve efficiency and business competitiveness. It allows companies to optimize resources, reduce risks, and ensure on-time, high-quality project delivery.
Project Cost Reporting
Cost reporting in Fluentis facilitates the performance analysis of projects. It allows businesses to compare current results with the initial plans, identifying both successful areas and those requiring improvement.
This process supports organizational learning and the optimization of future initiatives. Accurate documentation of project outcomes within Fluentis is also invaluable for reporting and compliance purposes.
This ensures that all regulations are met and that information is easily accessible for internal or external audits.
Controlling
The integration of Controlling in Fluentis provides quick access to economic and operational data. This means that managers and decision-makers can make informed decisions based on concrete facts, minimizing the margin for error.
Controlling in Fluentis enables the definition of key performance indicators (KPIs) and continuously measures their achievement. This helps monitor business performance, identify critical areas, and pinpoint improvement opportunities.
Additionally, Fluentis simplifies the generation of reports and detailed analysis, providing a clear view of the company’s economic and operational status. This is essential to ensure financial sustainability and market competitiveness.
Controlling in Fluentis is not only about monitoring but also about planning and forecasting. It helps to develop long-term strategies, manage risks, and optimize resource allocation.
Controlling within Fluentis provides the transparency necessary to make informed decisions, measure performance, and plan for the future. It is a strategic investment that pays dividends in terms of efficiency, profitability, and business success.
Batch Management
Batch management is one of the best methods for organizing operational processes. Raw materials, work-in-progress items, and shipment units are identified by creating unique batches, which can be distinguished by creation date, origin, or other criteria. In Fluentis, batch management, integrated with UDC management, ensures that companies requiring traceability between finished products and raw materials can maintain that connection.
Thanks to these management systems, it is much easier to verify data accuracy and track the flow of materials throughout operational processes. The logistical efficiency of the ERP system is also improved when using an integrated WMS, such as Fluentis Mobile.
A correct batch identification and the subsequent organization of operational processes are crucial for businesses in sectors where traceability is an essential requirement. For Fluentis, it is important to balance accuracy with functionality, ensuring both tracking and operational speed. For this reason, we have already developed BPMN processes to propose the best usage scenarios for our software and its features.
Industry 4.0
The interconnection between Fluentis and Industry 4.0 machinery is a pivotal element for the optimization and digital transformation of industries. Industry 4.0 is characterized by the integration of digital technologies into production processes. This integration enables companies to achieve enhanced operational efficiency and smarter resource management.
Fluentis serves as the “heart” of the company, managing business activities such as resource planning, order management, inventory, and accounting. Industry 4.0 facilitates real-time data collection and analysis from devices, sensors, and machinery, improving visibility and automation of production processes. Integrating this data into Fluentis allows for more accurate and timely planning, reducing machine downtime and optimizing production flow.
The interconnection promotes transparency across the entire supply chain, enhancing collaboration with suppliers and customers. This leads to greater responsiveness to market demands and improved inventory management.
Utilizing AI within Industry 4.0 can enhance predictive maintenance, enabling proactive interventions and reducing unexpected downtime. Fluentis can integrate with these systems to automate maintenance operations and optimize spare parts inventory.
Real-time data analysis enabled by Industry 4.0 allows Fluentis to provide more accurate and immediate reports and dashboards, assisting executives in making informed strategic decisions. Additionally, the interconnection facilitates customized production and product personalization to meet specific customer needs.
The integration also supports better quality management by enabling Fluentis to track production information, quickly identifying defects or anomalies in the production process.
In conclusion, the interconnection between Fluentis and Industry 4.0 machinery offers significant opportunities to enhance efficiency, agility, and competitiveness in industries. Integrating these technologies allows for smarter resource management, more flexible and customized production, and improved analysis and utilization of business data. In Fluentis, interconnection can occur through various tools: Bizlink, Frontier Database, or WebAPI.
MES or Advanced Progress Dashboards
Fluentis ERP’s integrated Manufacturing Execution System (MES) is designed for direct use by operators on the shop floor. Its user-friendly interface, compatible with traditional PCs, touch monitors, or tablet PCs, enables operators to:
- Monitor production sequences
- Access production documentation
- Record time logs and machine downtimes
- Report quantities produced or non-compliant
- Log quality control checks
- View production KPIs, performance metrics, and Overall Equipment Efficiency (OEE)
- Print product identification labels
This integration ensures real-time synchronization with Fluentis ERP, enhancing operational efficiency and providing comprehensive insights into production processes.
about Fluentis’s integrated MES and how it streamlines production management.
Assemblies / Assemblies / Machine Side
With Fluentis, it is possible to manage the assembly and commissioning of specific plants at the construction site, thus managing the machine side.
Fluentis allows managing individual customer projects both with a preventive bill of materials for the machine side, which is different from the internal production bill of materials, thus planning material procurement for external interventions, planning resources and personnel, managing travel documents and business trips, and reporting expenses and interventions.
For each individual project and plant, there is a trace of the individual components used to intervene correctly in post-sales.
Integration with PDM
The integration between PDM (Product Data Management) and Fluentis: These two systems, when properly combined, can represent a milestone in optimizing business operations and promoting sustainable growth.
The integration of PDM and Fluentis offers numerous advantages. First of all, it improves operational efficiency by providing a complete, real-time view of product and business process information. This reduces errors and accelerates production.
Additionally, the integration fosters greater collaboration between departments, as everyone has access to accurate and updated data. This promotes internal communication and strategic alignment. The integration between PDM and Fluentis can contribute to better customer satisfaction, as it leads to a greater ability to respond quickly to market needs and customize products.
In conclusion, the integration between PDM and Fluentis is a strategic move for any company that wants to remain competitive in an increasingly complex and interconnected world. Investing in this integration means improving efficiency, internal collaboration, and customer satisfaction. It is a fundamental step towards long-term business success.
Discover how Fluentis ERP
can transform your business
15-day free trial | No automatic renewal | Instant access
Contact us for more information
Get in touch with us if you:
- Are a SME in Manufacturing, Distribution, or Services
- Need to streamline and digitalize your business processes
- Want to take advantage of the benefits of a native cloud solution
- Want to replace your non-integrated softwares with a unified ERP platform
+1 281 404 1726
Chat with us