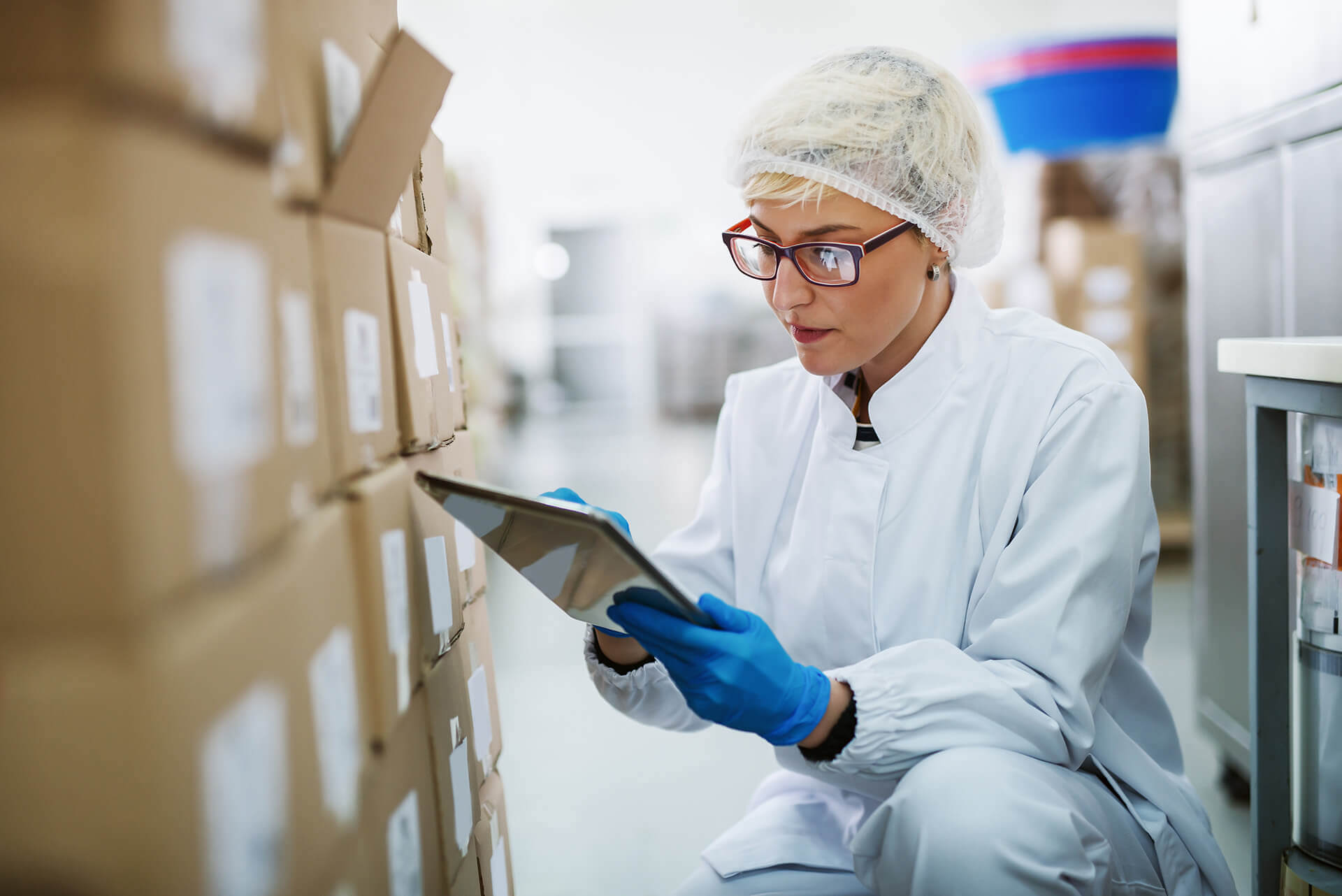
Aim for Top-Quality Standards to Outperform the Competition
Plan and Control Product and Process Quality with a Robust Quality Management System
The Quality Management Area in Fluentis ERP includes a comprehensive set of procedures designed to provide organizational support for both product manufacturing and service delivery. It also aids in managing personnel dedicated to achieving quality policy objectives.
In today’s competitive business environment, maintaining high-quality standards and meticulously managing related procedures are critical.
The integrated Quality Management System (QMS) module in Fluentis ERP enables precise control over product manufacturing, incoming material inspections, and non-conformities. It also supports supplier evaluation and the implementation of corrective actions to enhance service quality, improve customer satisfaction, and align with ISO 9001 standards.
In Fluentis ERP, Quality Management is seamlessly integrated with all operational areas.
Modules and FeaturesStrenghts
Management of both internal and external documents
Technical Sheets, Control Plans, Item Inspections, and Certificates of Analysis
Complaints and Non-Conformities
Corrective Actions
Calibration of Measuring Instruments
Supplier Qualification
Personnel Management
Step-by-Step
Quality Control
The first essential step in product and material quality control is defining Control Plans. These plans outline the measurements to be taken, the instruments to be used, the target values, and the acceptable limits that determine compliance. The measurements verify that homogeneous groups of items fall within the specified property ranges.
Control Plans, which can be customized for each customer or supplier, define both acceptance inspections and in-process checks. Measurements performed on an item or a batch of purchased or processed items are stored in the Item Inspection record.
Another key document is the Product Technical Sheet, used to list all the technical and physical-chemical characteristics that qualify a product as suitable for a specific function or application. This applies to both standard products and customized items tailored to client requirements.
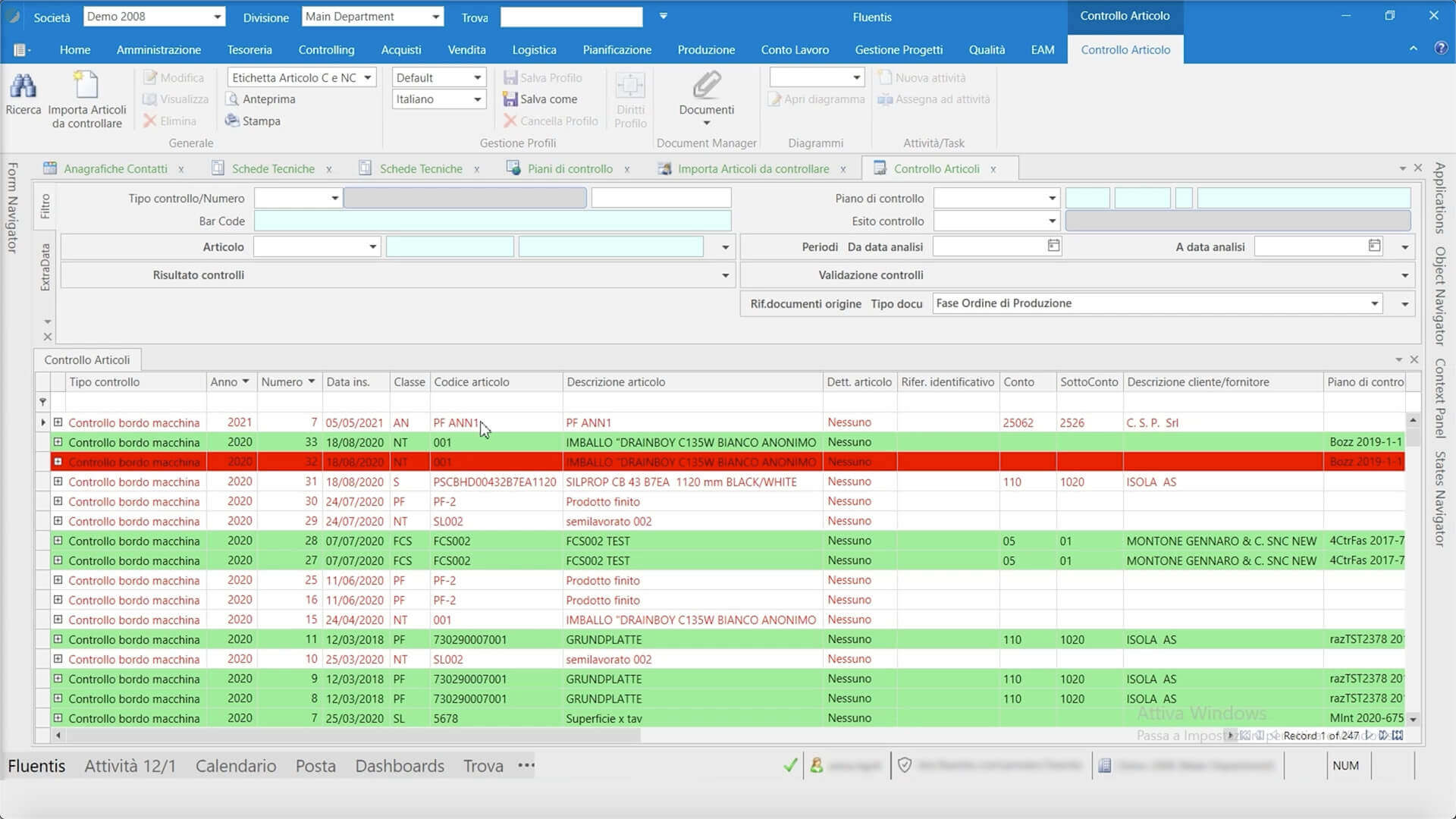
Conform or Non-Conform? The System Will Tell You
With Fluentis, the item can be controlled throughout its entire workflow, ensuring traceability.
Control can occur at various stages: when receiving goods, acquiring the delivery note (DDT) or purchase invoice, in different production phases, during returns from subcontracting, and throughout all warehouse movements.
Each Item Inspection is linked to a Control Plan, inheriting the defined limits. The system identifies the operator performing the test and, based on the values entered, automatically determines whether the result is compliant or non-compliant.
At the end of each test, the system allows you to declare which items passed and which failed the inspection, generating the corresponding warehouse records. Lastly, with the Certificate of Analysis, the analysis results and compliance with the values are certified.
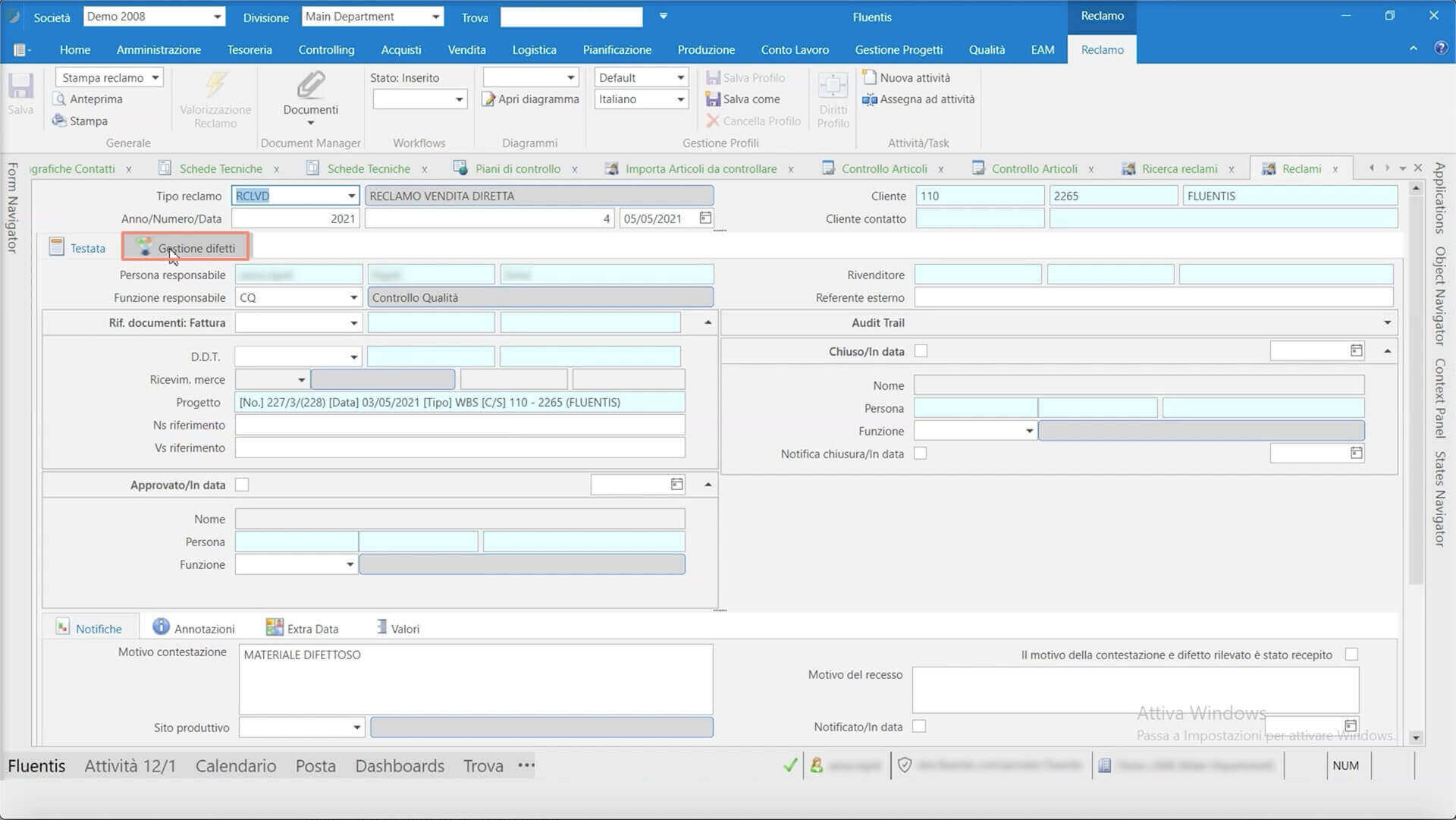
Complaints and Defects
Sometimes, a control may be missed, leading to a customer complaint. With Fluentis, we can resolve the issue efficiently.
In Complaint Management, different predefined complaint models are handled. For each type of complaint, a corresponding default credit note type for customer returns is defined.
In conjunction with Complaint Management, the Defect Management module tracks the identified defect, its suspected cause, the production stage where it was found, the actual cause of the defect, severity, the proposed technical solution, and the corresponding commercial resolution.
For each defect, a corrective action can be associated to resolve the issue or prevent it from recurring. You can list the objects being reclaimed, detailing batch numbers, serial numbers, or units of delivery, including quantities, costs, and return data. It also allows tracking of materials used for repairs, identifying involved parties or functions responsible for managing the complaint.
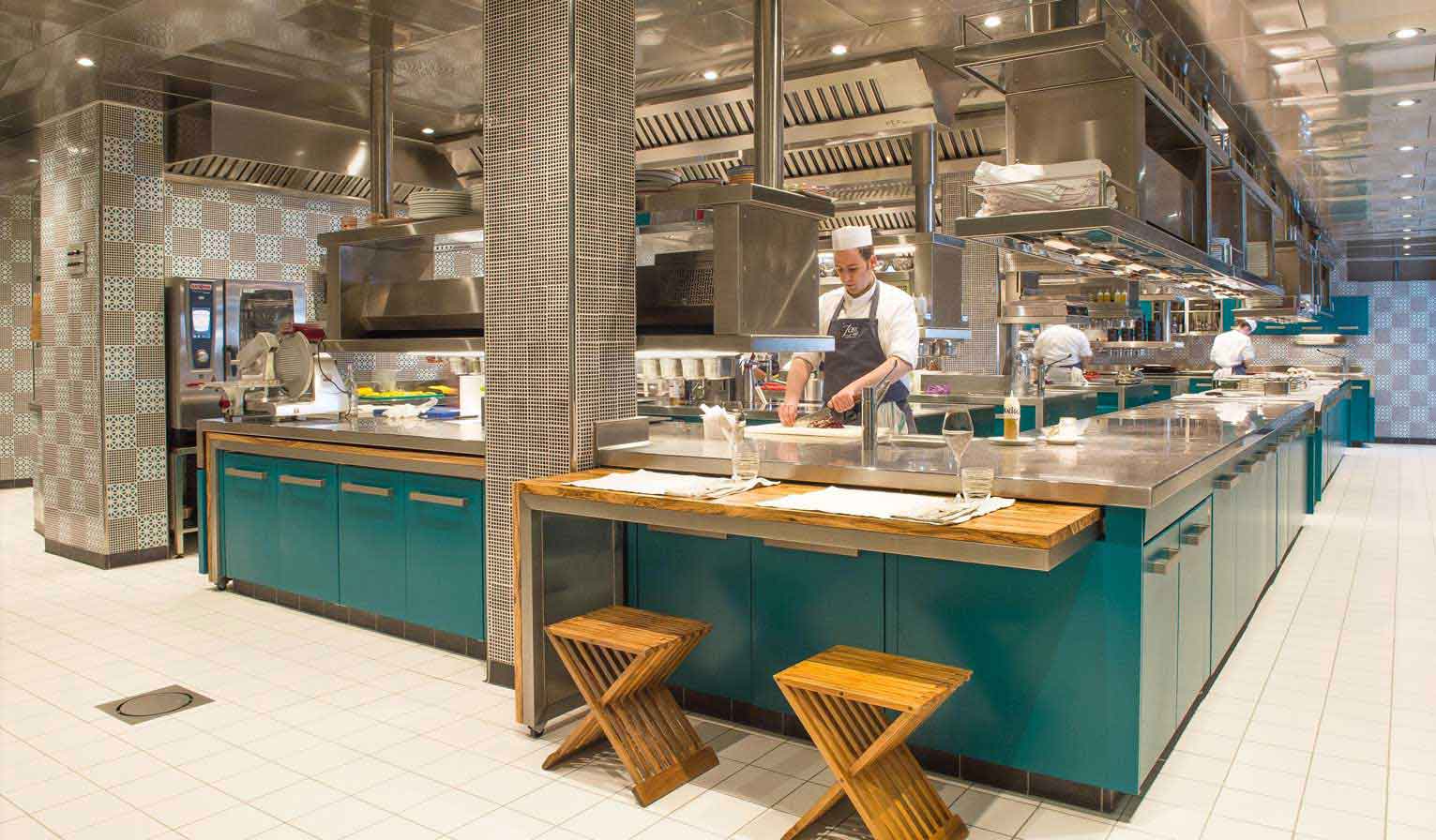
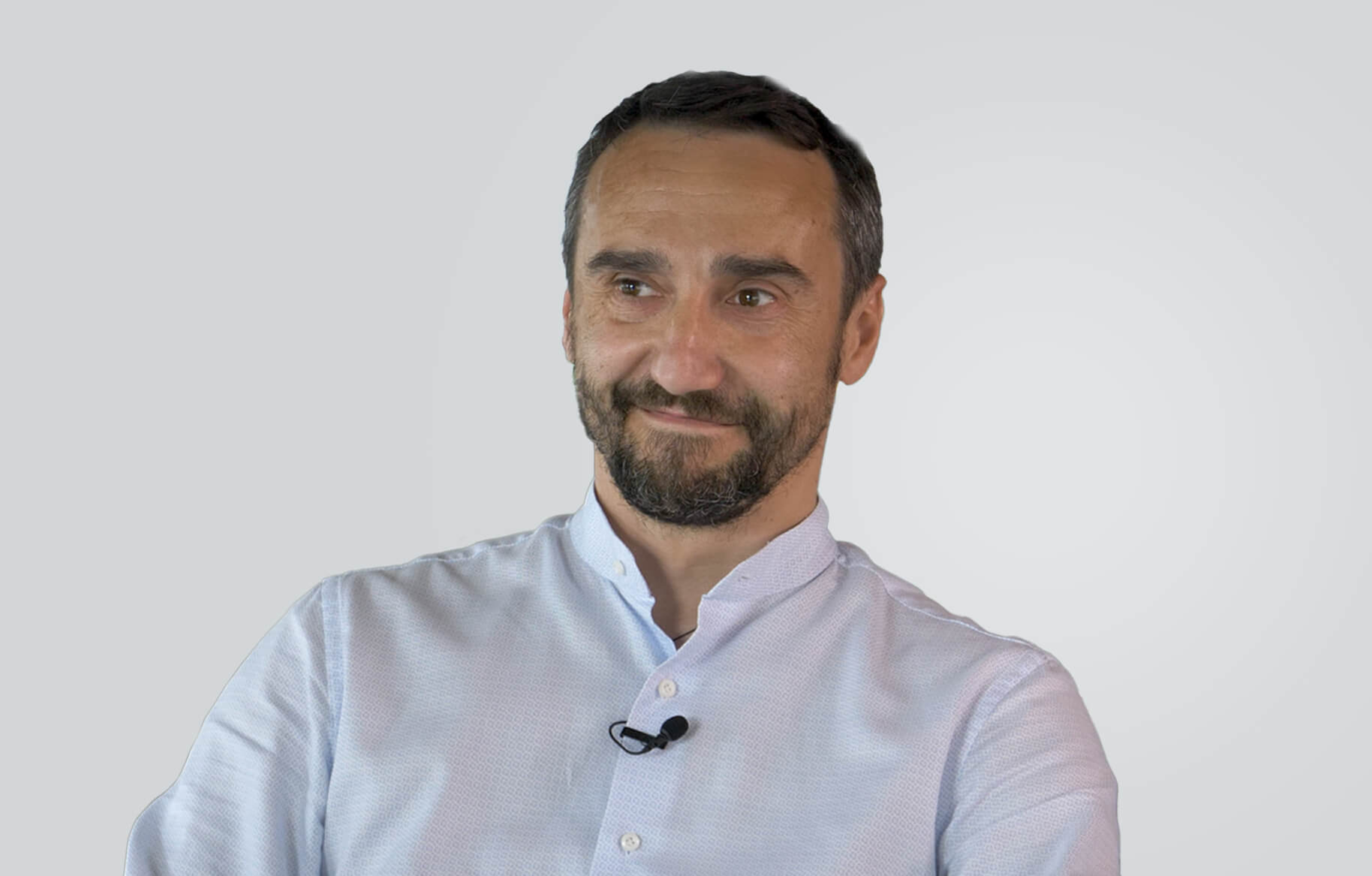
What our customers say about Fluentis
Con l’introduzione di Fluentis ERP e dei suoi Add-On nativi, Marrone riesce a gestire in modo integrato tutte le funzioni aziendali con un alto livello di automazione e di efficienza sia nella raccolta dati, sia in ambito produttivo che nella qualità che ci rende più agili nel soddisfare le esigenze specifiche dei nostri clienti
- Maurizio Fantin, Titolare
Marrone Srl
External Origin Documents
The system allows for the cataloging of all documents coming from external sources. These documents can be categorized into various types: Laws, Standards, User and Maintenance Manuals, Regulations, Declarations of Conformity, Technical Specifications, Safety Data Sheets, etc. Access rights and distribution lists are inherited from these categories. Documents can be easily attached by dragging and dropping them.
Features
- Assigning documents to a specific location for immediate traceability.
- Distribution to relevant company functions.
Internal Origin Documents
The system allows for the cataloging of documents originating from internal sources within the company. These documents can be categorized into various types: Manuals, Organizational Charts, Processes, Procedures, Supply Specifications, Operational Instructions, etc. Access rights and distribution lists are inherited from these categories. Documents can be easily attached by dragging and dropping or created using the integrated document generator.
Features
- Management of editions/revisions.
- Assigning documents to a specific location for immediate traceability.
- Distribution to relevant company functions.
Item Control
The module allows for the cataloging and recording of all the information necessary to ensure that production and service delivery occur under controlled conditions:
- Technical Sheets catalog all the information describing the product’s characteristics as suitable for a contract, functional specification, or a specific application.
- Control Plans catalog all the activities and measurements required, as well as the values to be achieved, to ensure that materials and products fall within the limits of the properties specified in the Technical Sheets.
- Item Control enables the recording of the measurements taken, the values recorded, and the subsequent indication of whether the material or product being checked is compliant or non-compliant.
- Analysis Certificates confirm that the analysis has been performed and that the values specified in the Technical Sheets or customer specifications have been met.
Features
- Integration between the purchase, subcontracting, and production modules.
- Technical Sheets, Control Plans, Item Control, and Analysis Certificates.
- Availability of sampling plans, operational instructions, and control charts.
- Issuance of Analysis or Test Certificates.
Complaints and Non-Conformities
These management processes arise from the specific need to increase customer satisfaction by improving the quality of products and services, as well as meeting regulatory requirements and efficiently collecting, cataloging, and retrieving reports.
The management process not only covers the handling of complaints but also the management of returned products and service disruptions. The information, carefully collected and analyzed, can provide valuable insights into defects and process shortcomings.
Features
- Standard defect and cause management models, along with integrated 8D problem-solving methodology.
- Integrated generation of debit and credit notes.
- Integrated generation of corrective actions.
- Pareto analysis of defects and causes.
- Integration with the purchasing, subcontracting, and production modules.
Corrective Actions
This document catalogs the actions aimed at reducing or eliminating the causes of non-conformities, in order to prevent their recurrence. It allows for the recording of evaluations to verify whether the actions have achieved the intended objective.
Features
- Review of non-conformities.
- Identification of the causes of non-conformities.
- Evaluation of the need to implement actions to ensure that non-conformities do not recur.
- Determination and implementation of necessary actions.
- Recording of the results of implemented actions.
- Assessment of the effectiveness of the actions taken.
Calibration of Measuring Instruments
This module allows for the cataloging and periodic or extraordinary maintenance of monitoring and measuring instruments used to ensure the suitability of products and the delivery of services. Internal calibrations and calibration certificates from third-party organizations can be planned and recorded.
Features
- Cataloging of all instruments suitable for monitoring and measuring the product to ensure compliance with required specifications.
- Planning of calibration activities.
- Calibration expiration alerts.
- Recording of external calibration certificates and internal calibrations performed.
Supplier Qualification
This management module assists the company in selecting and evaluating suppliers based on their ability to provide products or services that meet the organization’s requirements. It involves assigning key supplier information, setting criteria for selection, evaluation, and re-evaluation.
Features
- Periodic supplier evaluations.
- Analysis of the claimed value relative to total sales for a given period.
- Analysis of non-conformities reported.
- Analysis of supplier adherence to delivery timelines.
Discover how Fluentis ERP
can transform your business
15-day free trial | No automatic renewal | Instant access
Contact us for more information
Get in touch with us if you:
- Are a SMB in Manufacturing, Distribution, or Services
- Need to streamline and digitalize your business processes
- Want to take advantage of the benefits of a native cloud solution
- Want to replace your non-integrated softwares with a unified ERP platform
+1 281 404 1726
Chat with us